Last we spoke, you were working in the offgrid field and making modules for solar street lighting. How would you describe the company’s focus now?
We are still in solar street lighting and we work with market leaders. More generally we’re making customized modules, and since we started, we have made 7 million modules or more. All our modules go to battery systems – we call it the “self-charging devices” segment. Then we have “energy access” customers with pay-as-you-go services. Vehicle integration is a new one that is coming up – it does work a bit differently.
E-mobility: On a greener road to transportation
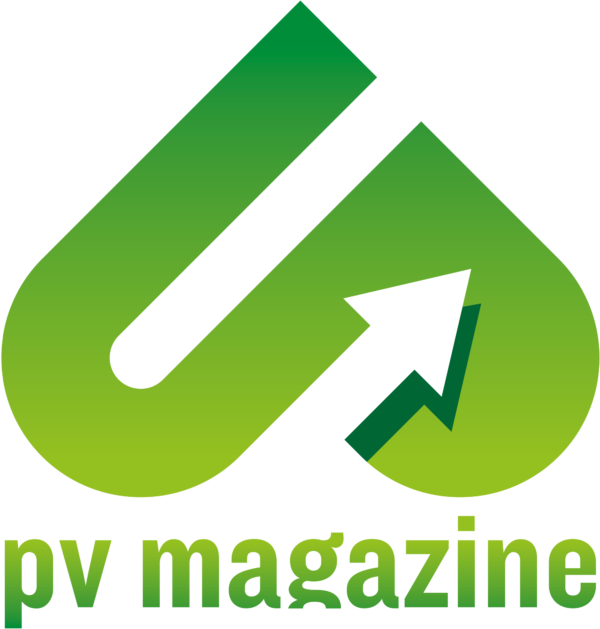
So, how have you approached VIPV?
We started [on VIPV] four to five years ago with Fraunhofer CSP with research projects. From a principles perspective, we think this is huge. [In EVs| there is a battery and solar, which means Opes is in a good place. There is also a lot of surface area [for solar] if you combine all the vehicles together.
Our approach from a technical perspective is that we are solar cell independent – we can use n-type, TOPCon, PERC mono. And we try to make these cells feasible for the harsh conditions in the vehicular environment – vibrations, impacts, bended 3D surfaces, interconnections. We have worked on these and have now come out with the first market-ready products.
How did you approach manufacturing to meet these challenges?
Compared to the standard module industry our whole business is very different – solar is a component. In the vehicle sector it is a bit more sophisticated because the conditions are new, there is a lot of regulation, and it has a longer process in development. There are usually institutes to work with, the vehicle industry, and several partners like sub-suppliers. It is a complex process.
I imagine it’s a different type of production. Regular module production is about relentlessly driving out cost and achieving huge production volumes. How would you describe the challenges in VIPV production by comparison?
It is a very different industry. You must go quickly from manual production to produce samples, to pilot production, and then develop automation station by station. When you are at scale, as we are in the share bike segment, then there is a production line that is fully automated – in this case it is a 6W FR4 module. This competence you can only have when you are used to it and used to producing several products at the same time.
You need to develop partly your own production equipment or modify existing equipment, put it into the line quickly and ensure it performs at an optimal level. That is our core competence, and we are bringing it to the vehicle-integrated PV sector. In the end, there will not only be one VIPV module, but many, with partly 3D elements with flexibility and molding.
We have a supply chain setup that is not only dependent on one PV source. We go with 95% standard cells from the PV industry and make these fit for the sector because then we also benefit from the continuous efficiency increases, driven by the PV industry as a whole – and not working on one specific technology on the cell level just for vehicles and then have to scale that.
Is thin-film PV suitable or are you more convinced by crystalline silicon?
We do try to get rid of the disadvantages of crystalline cells.
As in, they love to crack?
They do love to crack. And you have to really embed them in a way that they don’t do this – and there are ways and we have figured this out. You can actually bend crystalline cells quite far and we run really hard vibration tests and they survive and survive well. We have also made a lot of progress on the homogeneity, and with back-contact cells you have this nice black appearance. We have been able to overcome that standard cells look the same if you UV print the busbars with black – delivering very homogeneous modules based on standard cells.
In terms of production equipment, how do you work with your partners on tools that can deliver throughput but are also flexible?
Some equipment we buy or develop with equipment manufacturers, while others we develop from scratch. For example, we have a framing machine that is fully automated and flexible from 20W to 200W modules, fully developed by ourselves. For instance, we have one carmaker as a partner, and we deliver both the solar module for integration but also the semiautomated production line to integrate it into their line to apply it on the vehicle.
Going back to the big picture with VIPV and unlocking the mobility sector for the solar industry, what is your message about the opportunity and what can be done to avail ourselves of this opportunity?
Speaking of the potential, a back-of-the-envelope calculation shows that if 30% of buses, trucks and semi-trailers was equipped with solar, we are at 6GW to 7GW a year. I don’t think it will be GW inline production, which we know from the PV industry, but more medium sized companies that will become the classical suppliers of the car industry.
The car industry works with a lot of suppliers, and there is a new sector with PV as vehicle parts. In this context the skill you need is to go from R&D, into pilot, and then mass production and at speed. This requires a high innovation rate, a lot of cooperation between material, component companies, and solar together, so a new ecosystem. But it is not going to be a small niche.
This content is protected by copyright and may not be reused. If you want to cooperate with us and would like to reuse some of our content, please contact: editors@pv-magazine.com.