The manufacturing landscape in PV may appear to move at a glacial pace – even at the best of times. However, when certain market or policy signals spur manufacturers to act, things can change quickly indeed. This is true of both manufacturing in terms of geographic footprint, but also in terms of the technologies pursued.
Chinese PV manufacturers demonstrated this before, having established cell and module manufacturing facilities in countries like Malaysia and Vietnam, in order to avoid tariffs and other trade barriers, with impressive alacrity. Now, with new trade barriers looking likely to cause a major shift in the landscape due to the Section 201 trade case in the United States, Chinese manufacturers once again appear poised to take rapid action, and establish new facilities and potentially turn to n-type mono technology as their go-to cell architecture.
With the negatively doped side of the wafer forming the basis of the cell, n-type PV cells are an inversion of the mainstream p-type technology. Historically applied in back contact technologies, such as IBC cells, it has long been a niche PV cell structure, employed by high-efficiency and generally high-priced manufacturers such as South Korea’s LG or the United States’ SunPower.
With demand strong, high efficiency products incentivized under China’s Top Runner program and potential new facilities to be established in the U.S., n-type mono coupled either with PERT or HJT could emerge as a frontrunner for greenfield cell facilities.
But even before this occurs – and at the time of going to press it was uncertain as to whether sufficiently high tariffs on U.S. crystalline silicon (c-Si) PV imports would be imposed – the rush by developers and contractors to acquire modules has caused average selling prices (ASPs) to rise across the board. It has also presented major opportunities, both in the U.S. marketplace and further afield, to a host of manufacturers.
Sold out
During last month’s Solar Power International (SPI) trade show in Las Vegas, module suppliers with modules to sell were in short supply. GTM reported that most of the tier-1 module producers were sold out of 2017 production. And a host of new supply deals, some at impressive volumes, was also announced at this
year’s SPI.
China’s BYD revealed a 170 MW module supply deal with developer NextEra during the SPI show. The deal was originally upped from an initial 150 MW contract, after the extent of the tight module supply became apparent. BYD said that key to the sale was passing NextEra’s stringent quality tests. Home-grown U.S. c-Si suppliers are also benefiting from surging orders. Sunpreme, based in Sunnyvale, California, and with manufacturing facilities in China, announced a deal to supply
150 MW of its high-efficiency modules to True Green Capital Management (TGC). The deal is a massive one for Sunpreme, worth around three times the volume the company has supplied in its
entire history.
AT A GLANCE
- Robust H2 market demand is playing a role in driving high efficiency concepts such as n-type mono, including heterojunction (HJT).
- Trade barriers in the U.S. may lead to greenfield cell and module facilities in the U.S.
- Chinese manufacturers such as Jolywood are driving n-type mono technology forward.
- This article is part two in a series on high efficiency concepts, including HJT.
- Part one (pv magazine global 09/2017) focused on the equipment suppliers of key HJT production processes PECVD and PVD.
Sunpreme produces heterojunction PV cells and modules, which involves the deposition of very thin intrinsic and doped amorphous silicon layers onto either side of an n-type c-Si wafer. Sunpreme refers to its technology as Hybrid Cell Technology (HCT) and, like all HJT, is inherently bifacial.
Taking into account this bifaciality, which can be problematic due to a lack of standardization in rear side flash testing, Sunpreme rates its modules with an output of 380-420 W, in a glass-glass configuration.
And with the agreement, which was the first of its size for Sunpreme, the company has already indicated that it may very well look to expand its production capacity
inside the U.S. to fulfill the order.
“We expect that Sunpreme will expand its production capacity, ideally with a U.S.-based manufacturing facility that creates new U.S. high paying jobs in the solar business, while providing our Fund III limited partners with a secure source of high quality solar panels at attractive prices,” said TGC Managing Partner Panos Ninios – in a press release announcing the deal.
BYD, like a score of Chinese producers, is contemplating a move into U.S. manufacturing, although the company will delay any decision until after a determination in the Section 201 case is made. And while the 170 MW NextEra deal was for multicrystalline modules, when it comes to a future cell technology, it too is looking down the n-type HJT pathway – albeit cautiously.
From p to n?
Currently, BYD’s strategy has been to pursue multicrystalline technology, from ingot right through to module. Tom Zhao, the Managing Director of BYD’s Solar Division, says the company has an intense focus on cost, and that has driven its pursuit of multi to date. However, it is looking very closely at n-type mono, including HJT.
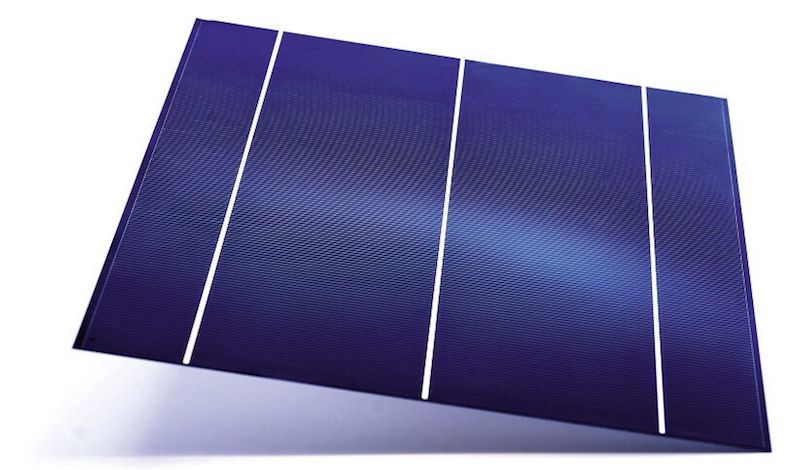
Image: IMEC
“When I think about mono and the right technology that can be achieved, it is n-type bifacial,” says Zhao. “That is really an amazing technology.” He goes on to say that n-type wafers can now be produced by a large Chinese producer at a very similar cost to multi wafers.
“But with n-type bifacial, the key advantage is the 0.1% LID [light-induced degradation],” says Zhao. “Immediately 2% degradation is avoided.” On the module front, BYD targets avoiding degradation, and in its dual-glass module deploys silicone encapsulant, thereby avoiding LID caused by the EVA degradation under UV light exposure.
In the wake of trade disputes and tariffs, Chinese leading cell producers such as JA Solar and JinkoSolar were able to establish cell production lines in Southeast Asia in astoundingly short time frames. Where what may have taken years in the past, it only took a matter of months. Given this need to move and execute quickly, delivery times for PV equipment providers must improve. Switzerland’s Indeotec is applying an innovative model to meet this challenge with heterojunction deposition equipment. Indeotec is partnering with third-party equipment manufacturers in Asia, with the Swiss team producing the PECVD reactors themselves, while the bulk of the equipment fabrication is outsourced.
“We are completely changing the model here,” says Omid Shojaei, Owner and CEO of the company.
“We would control the engineering, the R&D, reactor manufacturing, sales, assembly, and testing. Our suppliers are already qualified for Octopus II and now we are qualifying them for Octopus III.”
BYD says that by deploying the silicone encapsulant, 3% degradation is avoided, and when coupled with the n-type mono wafer, it makes an unbeatable proposition regarding power output over time. “So overall it is the best module in the industry,” says Zhao.
BYD will deploy its dual-glass silicone technology in its new Brazilian module facility, which was opened in early September and will have an output of
200 MW when fully ramped. With n-type mono bifacial cells, 400 W modules can be produced on the dual-glass platform – taking bifaciality into account – with a guaranteed 360-370 W on the front side as a baseline.
New momentum, markets
Chinese PV module producer Jolywood has been touting its bifacial n-type monocrystalline PERT technology of late, including at pv magazine’s Future PV Forum at Intersolar Europe back in June. Output has already begun, as modules rolled off an eventual 2.1 GW production facility located in China’s
Jiangsu Province.
The first sales of Jolywood’s bifacial n-type mono production have also been used as leverage into new markets. Last month, Jolywood announced that it would supply 6.775 MW of n-type mono PERT modules to India’s ACME Clean-tech Solutions Private Limited. Jolywood claims that it will be the first large-scale application of n-type mono bifiacial technology in India.
“The cooperation with ACME is only our first step in the Indian market,“ said Liu Yong, Jolywood Solar’s General Manager, in a press statement. “Double-side generation, zero LID, lower working temperature: With these features, Jolywood n-PERT products are very competitive for a high temperature environment such
as India.”
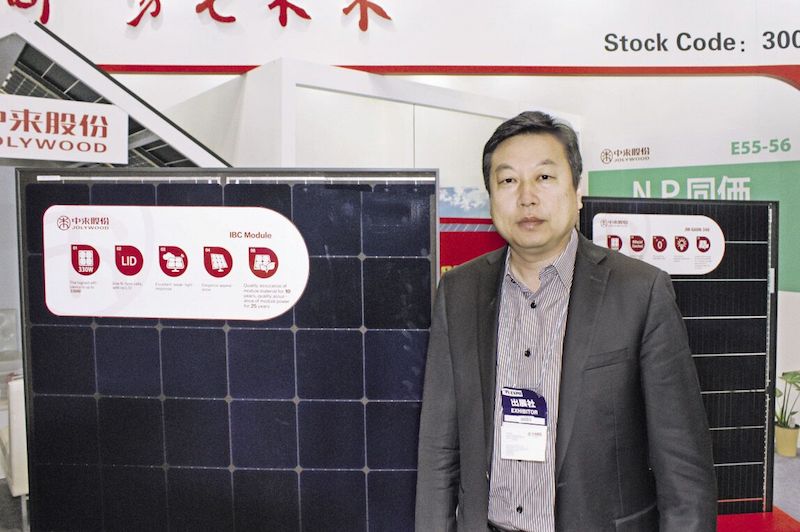
Jolywood is also looking to tackle a persistent challenge to securing a fair market price for bifacial modules. In July, it announced a collaboration with TÜV Nord and China’s National Photovoltaic Testing Center to advance the development of standards for the flashing of bifacial modules. The effort echoes the endeavors of a working group of European flasher suppliers that have been attempting to address this challenge for some years.
The challenge of optimizing materials for n-type mono production is also being tackled by Jolywood, this time through a strategic partnership with paste and technology supplier Heraeus. Jolywood deploys Heraeus’ SOL9360A metallization paste in its current production, and the companies indicated they hoped the collaboration would lead to the “next generation” of materials for high efficiency production.
At the Future PV Forum at SPI, the President of Heraeus Photovoltaics and Renewables Cluster, Andreas Liebheit, remarked to the pv magazine video team that “2017 has been the year of innovation launches. On a sequential time line you could say that now is the time to shift from PERC 1.0 to PERC 2.0 – the innovated PERC. We see n-type already coming up, but not on a mass volume – that will probably be the next generation.”
Next-generation PV concepts have a habit of appearing on the near horizon and yet remaining some distance away. On August 31, Tesla announced that it had begun the production of HJT PV cells at its Buffalo, New York manufacturing facility. The announcement was light on detail and big on chutzpah, as is Tesla’s wont, but nonetheless the move is encouraging – after some years in which it had appeared the company’s HJT production had stalled. The facility could be well positioned to supply the U.S. market if new c-Si solar PV tariffs eventuate, and conventional Tesla modules alongside its premium solar tiles could be sold.
Tesla, and originally SolarCity, had no easy time realizing production at the Buffalo fab. Having pivoted from its initially acquired Silevo HJT architecture to bringing Panasonic, the pioneer of the technology, on board to execute the project, it represents yet another step forward on the path to n-type mono moving from tomorrow’s technology, to that of today. S
This content is protected by copyright and may not be reused. If you want to cooperate with us and would like to reuse some of our content, please contact: editors@pv-magazine.com.