A group of researchers from Canada’s University of Western Ontario has developed and tested 3D-printed mounting mechanisms for the wood racking of PV modules. The open-source designs, aside from enabling distributed manufacturing, are also claimed to be cheaper and have a lower embodied energy and embodied carbon in comparison to conventional racking materials.
“Wood-based racks are especially appropriate for ground-mounted agrivoltaics but can be applied anywhere,” corresponding author, Uzair Jamil, told pv magazine.
According to the research group, wood racks also offer advantages such as ease of distributed manufacturing, a lower cost per W of materials, and no corrosion or rusting. “The problem with wood-based racking is that they do not enable the standard front surface attachments now common among proprietary aluminum racking systems. For the first time, this paper introduces novel 3D printed clamps for front-surface solar module mounting on wood racking structures,” they stated.
The researchers proposed four types of mounting mechanisms, which were simulated using the Abaqus software and the finite element analysis (FEA), which is commonly used to solve differential equations arising in engineering and mathematical modeling. Each mechanism was simulated as being printed using one of three common printing materials: polyethylene terephthalate glycol (PETG), acrylonitrile styrene acrylate (ASA), and polycarbonate (PC).
In all cases, the mounting mechanism was intended to support 410 W modules with dimensions of 1,880 mm x 1,042 mm x 40mm and a mass of 19.7 kg. They were also designed to utilize 127 mm long lag bolts with a diameter of 6.4 mm. A 7 mm wide hole is designed into all of the 3D-printed parts to accommodate the bolt.
The first mechanism was a T-shaped clamp, where the T-bar rests on the PV module’s frame and holds the module to the racking structure. In this case, a flat washer is placed between the bolt and the 3D-printed components to avoid damaging the clamp. Another proposal used a U-shaped clamp, which uses its own base to rest the module while a square washer holds the module from the top.
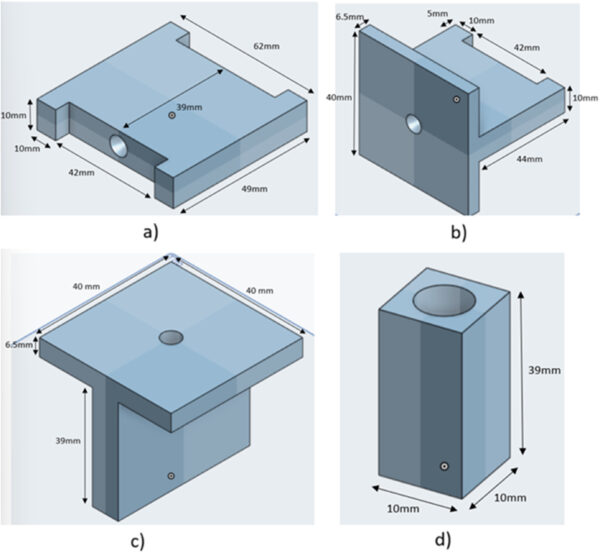
Image: SUniversity of Western Ontario, Renewable Energy, Creative Commons License CC BY 4.0
The following two mechanisms were spacers. In the first, a square spacer was used with a square washer to support the movement of modules. In the second, an H-shaped spacer was assisted by two square washers that held the solar modules, while the mount acted as a spacer between them.
“Among all the designs, the T-shaped clamp configuration showed better results with maximum stress on aluminum (Al) frame of 34.27 MPa,” said the researchers. “The highest stress was observed in U-shaped spacer for spacer (4.53 MPa – PC material), bolt (32.01 MPa – PETG material) and frame (37.30 MPa) and for washer in the H-spacer (42.77 MPa). Mises stresses for all the designs, however, are found within allowable limits qualifying the clamping technique to be adopted for future installations.”
Following the simulation results, the academics printed several mounting mechanisms to ensure their applicability in the field. “All the four clamps were relatively easy to install,” they stressed. “No installation issues were observed while tightening the lag screw. Using a predrill before tightening the lag screw, however, makes tightening/screwing operation easier.”
In addition, the group conducted an economic analysis of the production, accounting for the prices of the materials used for the printed parts, power consumption, time to print, electricity rates, cost of the washer, and cost of bolts.
“The cost of the different solutions presented varies from CAD1.50 ($1.10) to CAD3.83 for square spacer and U-shaped clamp, respectively,” they said. ”Available solutions in the market are mostly all metal clamps and sometimes even costlier, ranging from CAD 1.76/piece up to CAD4.50/piece. This is a 14.7% to 66% cost savings for the mounting clamps.”
The proposed mechanisms were presented in “Distributed Manufacturing for Distributed Generation: 3-D Printed Solar Photovoltaic Module Mounting Mechanisms for Wood Racking,” published in Renewable Energy.
“Our Free Appropriate Sustainability Technology (FAST) Research Group is currently working on completely 3D printed PV modules. We are also looking into the opportunity to make 3D-printed frames for frameless PVs,” said Jamil.
This content is protected by copyright and may not be reused. If you want to cooperate with us and would like to reuse some of our content, please contact: editors@pv-magazine.com.
This innovative approach to PV mounting highlights the flexibility of 3D printing for renewable energy applications. The clamp design cleverly addresses wood racking’s limitations – I’m particularly impressed by the weight distribution analysis. Would love to see long-term durability data after seasonal expansion/contraction cycles. For field technicians: how does installation time compare to traditional clamps?