Amid wide battery variety, each cell type and sub-species of device has unique vulnerability to degradation, influenced by usage and other factors. Some cells thrive at low temperature, others excel at high currents. Such specialization, however, often comes at a cost.
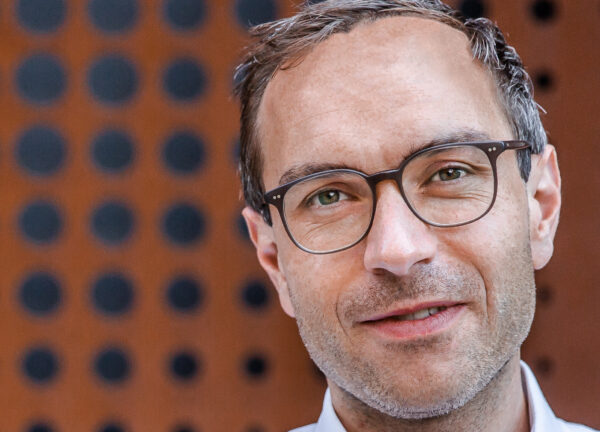
Image: volytica diagnostics GmbH
Battery aging is either related to time (in cases of calendar or “calendric” aging) or to usage, with charging and discharging representing “cyclic” aging.
Both forms of aging contribute to capacity and efficiency fade and increasing internal resistance as ions become trapped in unpleasant side-reactions for good. These reactions are driven by various “influencing factors.” Typically, ions react irreversibly with other materials in the cell, forming passive residue and preventing their use for energy transport.
Common influencing factors – whose impact varies by cell type – include the temperature of battery cells; device state-of-charge (SOC); and the current, or power, used during charging and discharging. Regarding state-of-charge – the amount of charge, or energy, in a battery – idle SOC matters when a battery is not in use and the SOC window (the range in which cycling occurs) is relevant when a device is cycling.
Mechanical stress, such as vibration and pressure, is another influencing factor in battery degradation but we’ll focus on the three factors above for now.
Temperature
Temperature plays a pivotal role in battery life. Most cell chemistries benefit from storage and idling at low temperatures, below 20 C, as that slows calendric aging by reducing the chance of side reactions. Idling at higher temperatures can greatly increase the degradation rate.
Conversely, most cell technology is very sensitive to low-temperature operation, causing a dilemma. With more than 30 C to 40 C being less than optimal, the sweet spot for battery cell operation is around 15 C to 25 C, for most chemistries. Newer nickel-manganese-cobalt (NMC)-based batteries are very sensitive to low temperature charging and dangerous defects can occur if charging at lower than 10 C. In the graph to the left, showing three high-quality NMC cells of the same type, the rate of degradation is slightly improved by reducing the operating temperature by 10 C, from 25 C (the orange line) to 15 C (violet line). Going 10 C lower (blue line), however, would crash the battery almost immediately.
Lithium plating
Lithium-ion (li-ion) batteries are generally safe but under certain conditions – in cold temperatures, under high current, or with an already well-filled host electrode – they can experience lithium plating. The example above showcases the impact of plating at low temperature. Plating is a form of residue that occurs when lithium ions form metal deposits inside battery cells. Over time, this process can accumulate and eventually lead to internal short circuits that might trigger a thermal runaway – a rapid and dangerous release of heat and gases.
It's important to note the conditions which facilitate plating are only partially controllable by a battery management system (BMS). Operators must take responsibility for monitoring and maintaining their devices.
SOC
State of charge has a substantial impact on battery lifetime. Both idle SOC, during non-usage (which concerns calendric aging), and the SOC range or window during operation (cyclic aging) matter. The following example shows two identical NMC cells.
The graph below shows the degradation evolution of two almost identical use cases of a high-quality NMC cells.
Both use only around 50% of the battery, and the first use case (the blue line) does so in the upper half of the SOC, starting fully charged and falling to 50% before being fully charged again. The second use case (in orange) starts at 50% charged and ends virtually empty. As the graphs show, the impact on degradation is incredible: the orange battery will live two times to three times longer than the blue one, reducing total cost of ownership by more than half.
It should be stressed, however, this is an example of a particular cell type and other devices and cells may behave completely differently. As a rule of thumb, avoiding an SOC above 90% and below 10% generally extends battery life, but there are exceptions.
Battery stress levels
Assessing battery stress can be complex, even for experts, and can be affected by temperature changes, SOC ranges, and the profile of a device’s C-rate – its rate of discharge relative to maximum storage capacity. Such factors interact intricately with the susceptibility matrix of cell types. Stress level is a single number which gauges how stressful a battery usage profile is, compared to a reference case.
A stress level of 1.0 indicates usage is roughly as stressful as planned, 2.0 suggests a device will degrade about twice as fast as expected. Tools such as battery diagnostics automatically analyze stress levels, helping risk assessment and optimizing usage profiles.
BMS'
There's an ongoing debate about whether BMS’ should control influencing factors to maintain battery health. BMS’ can prevent particularly damaging and dangerous usage but don’t typically provide recommendations for optimizing stress levels.
Future batteries
The global battery trend toward higher energy density for longer ranges often comes at the cost of reduced device lifetime. Battery lifetime and safety margins have, on average, retreated in recent years. That means extra care should be taken when operating the most expensive degrading component of the energy transition. The susceptibility of all li-ion cell types to influencing factors should make us aware of the untapped optimization potential in many battery usage scenarios.
Importance of monitoring
The complexity of stress factors and battery usage cases highlighted above ensures simply counting cycles or logging a device’s age will not give a clear picture of its degradation. It is clear that regularly checking battery capacity and state of health is essential and we can see that slight adjustments to usage profiles can significantly reduce battery stress and extend asset lifetime by 10% to 50% or more.
Volytica diagnostics will be holding a pv magazine webinar about batteries and their deployment in the energy transition, at 4 p.m. CET tomorrow.
About the author: Claudius Jehle is founder and CEO of Volytica diagnostics GmbH, a company focusing on easy, safe, and independent battery quality and health assessment. Claudius studied mechanical engineering and system identification at TU Munich and TU Delft and led the energy storage diagnostics and telematics research group at the Fraunhofer Institute for Transportation and Infrastructure Systems IVI, in Dresden, until the spin-out of Volytica in 2019.
The views and opinions expressed in this article are the author’s own, and do not necessarily reflect those held by pv magazine.
This content is protected by copyright and may not be reused. If you want to cooperate with us and would like to reuse some of our content, please contact: editors@pv-magazine.com.
1 comment
By submitting this form you agree to pv magazine using your data for the purposes of publishing your comment.
Your personal data will only be disclosed or otherwise transmitted to third parties for the purposes of spam filtering or if this is necessary for technical maintenance of the website. Any other transfer to third parties will not take place unless this is justified on the basis of applicable data protection regulations or if pv magazine is legally obliged to do so.
You may revoke this consent at any time with effect for the future, in which case your personal data will be deleted immediately. Otherwise, your data will be deleted if pv magazine has processed your request or the purpose of data storage is fulfilled.
Further information on data privacy can be found in our Data Protection Policy.