A group of scientists from the Silesian University of Technology in Poland has developed a compressed air energy storage (CAES) technology using a thermal energy storage (TES) system built into a disused mine shaft, which is effectively repurposed as a compressed air tank. “Our storage concept is aimed at reusing and protecting the post-mining underground infrastructure, which very often, after the closure of the mine, is irretrievably devastated,” the research's corresponding author, Łukasz Bartela, told pv magazine.
The group sees these mining sites as having potential for low-cost energy infrastructure. “Mine shafts are usually located in proximity to power plants and/or distribution stations,” the research group stated. “This allows the use of existing grid connection infrastructure. In addition, proximity to highly industrialized areas reduces energy transmission losses. The lack of requirement to build an aboveground TES storage tank economizes the limited space available.”
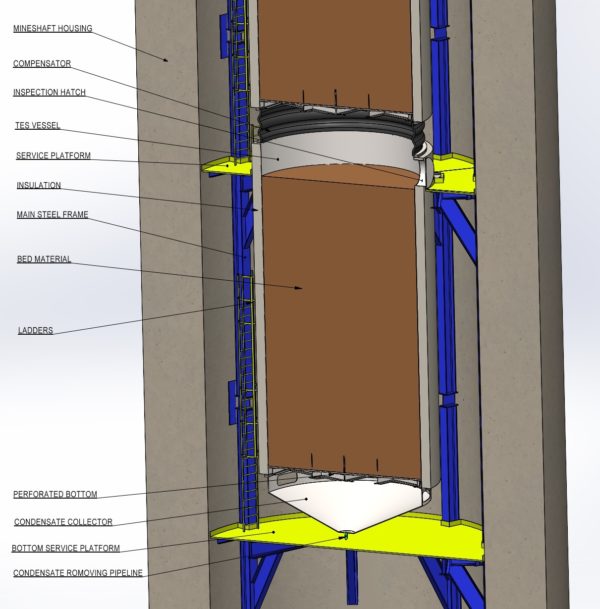
Image: Silesian University of Technology
The system works without using external heat sources, and utilizes an air compressor, a compressed air reservoir with a built-in thermal energy storage system, and an air expander. The elements of the system can be either one- or two-sectional.
In the proposed system configuration, the TES tank is embedded and attached to the shaft casing. This helps reduce heat loss, even when the heat leaves the accumulation material and goes through the air in the shaft reservoir. The TES system itself is adapted to the geometry of the shaft, and the heat conduction field is reduced, which has a positive effect on the energy efficiency of the heat storage process.
“The greatest advantage of placing the TES system in the volume of the pressure reservoir is the possibility of using a thin-walled shell structure in which the thermal energy storage material is placed,” Bartela further explained. “This allows for a significant reduction in the cost of the TES system.”
Steel cylinders with a perforated underside are used to divide the tank into segments, which allows easy installation and periodic inspection of the heat-absorbing material bed. “Communication between the sections will be possible using ladders, which are also part of the TES vertical positioning system,” the scientists specified.
At the charging stage, electricity is used to drive the compressor. The hybrid underground system is charged with hot, compressed air injected into the reservoir through an inlet pipeline with a built-in shut-off valve. The air then flows through the TES system, heating the storage material.
In the discharge phase, air flows through the TES system taking heat from the accumulation material. Then, the hot air goes to the expander, which drives the generator that produces electricity. “It is advantageous to fill the TES unit with a suitable heat-accumulation material at a sufficient volume to absorb the heat, this is important for the high degree of cooling of the stored air,” the group emphasized. “By limiting the temperature of the storage air in contact with the underground reservoir shell, heat losses will be reduced and, as a result, the CAES system energy storage efficiency will be increased.”
They calculated for a compressed air storage facility with a volume of 60,000 m3 and a maximum pressure of 5 mega pascals (MPa). Based on this they calculated the facility's energy storage capacity at 140 MWh, round-trip efficiency of around 70%, and energy efficiency of 95 % for the heat storage tanks.
They also explained that, in exceptional situations, it is possible to maintain the air at a pressure of up to 8 MPa, depending on the specific characteristics of the mine shaft. “In this case, the energy capacity of the system may exceed 200 MWh,” Bartela emphasized. “The use of common rocks such as granite or basalt in the TES system will be most advantageous from an economic point of view. Currently, however, research is conducted at the Silesian University of Technology on alternative synthetic materials.”
The group introduced the energy storage concept in the study Evaluation of the energy potential of an adiabatic compressed air energy storage system based on a novel thermal energy storage system in a post mining shaft, which was recently published in the Journal of Energy Storage. “We are currently working only on optimizing the design of the heat storage tank, which could reduce the cost of the TES module,” Bartela concluded.
According to the group, there are 139 shafts in active coal mines in Poland and also 34 shafts in active copper and rock salt mines. Currently, 39 are scheduled for decommissioning, about half of which is used for pumping water. The deepest shafts are over 1,300 m deep.
This content is protected by copyright and may not be reused. If you want to cooperate with us and would like to reuse some of our content, please contact: editors@pv-magazine.com.
I would love to help with the project and assimilate the technology in cities in residential building areas.