Europe remains one of the largest solar installation markets globally; however, its once-thriving manufacturing base ground to a halt around a decade ago as Asian competitors outpriced and out supplied their European peers at eyewatering speed.
With solar deployment levels continuing to ramp up, and sustainability issues coming increasingly to the fore, calls for meaningful domestic manufacturing capacity to be re-erected have grown louder over the past few years. 2022 might be the time they are answered.
Last April, the European Solar Manufacturing Council (ESMC) said that at least 75% of PV demand in Europe should be covered by domestic production. However, as pv magazine outlines in the upcoming March issue, in 2020, Europe had 22.1GW of polysilicon production capacity in operation, but just 1.25GW of solar wafer production capacity, 650MW of solar cell capacity, and 6.75GW of solar module production capacity, based on figures issued by the Fraunhofer Institute of Solar Energy Systems (ISE) in its 2021 Photovoltaics Report. Thus, the industry has a way to go if it is to achieve meaningful capacities.
In the following interview, Johan Lindahl, ESMC secretary general talks to pv magazine about the current state of play, the challenges and opportunities facing European solar manufacturers, and the plans that have been identified to achieve GW-scale capacities.
European manufacturing
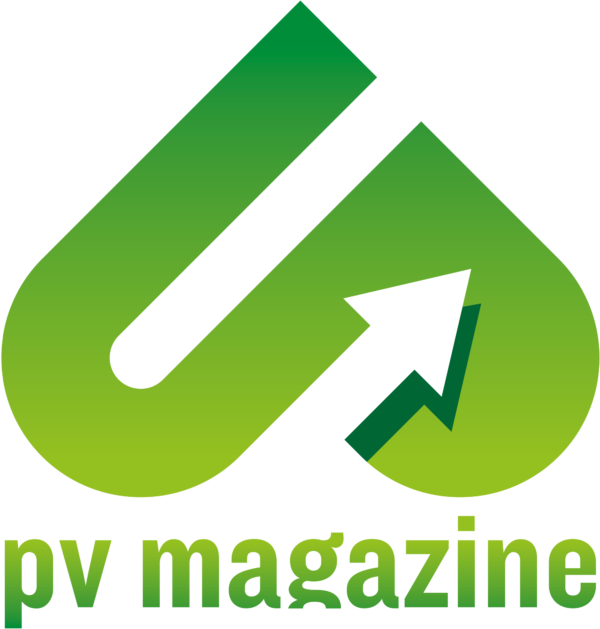
pv magazine: What challenges do European manufacturers face? Where are the opportunities?
Johan Lindahl: We have identified several challenges for the competitiveness of the European PV manufacturing industry:
- Invisible, but extensive grants, loans, credit, and tax support in China.
- Visible and extensive grant support in the US and India.
- Limited market deployment of EU PV innovations in the local market and not properly protected IP and Patents in external markets.
- Strict European PV manufacturing and labor standards that are not reflected by the respective standards outside the EU.
- Potential higher PV components pricing and supply chain problems as a structural problem.
With regards to opportunities, we have identified several, including:
- Industrial PV production in Europe is starting to be cost-competitive. Recently, the price differences between European and Asian products have diminished due to current production and transportation costs and the significant increase in delivery times for Asian products. European PV manufacturing could be price competitive on two conditions: GW-scale PV manufacturing capacities and complete manufacturing value-chains in Europe. The EU needs to keep complete value chains for at least part of our needs without imports, notwithstanding the fact that imports will of course remain an important factor.
- Europe still holds a leading position in PV technology innovation, but this can only remain so if an industrial manufacturing base exists. The traditional aluminum back surface technology of solar cells (Al-BSF) with an energy conversion efficiency of 18-22% is currently being replaced by passivated emitter and rear contact (PERC) technology and its variants, which allows solar to achieve higher efficiencies of 20-24%, with only a moderate cost involved in upgrading production lines. The next step to third-generation high-efficiency PV cells will allow even higher efficiencies of 23-26%, based on heterojunction (HJT) or TOPCon technologies. These can be produced today at a similar cost to PERC cells, in the 20-30 euro ct/Wp price range, resulting in competitive or even lower LCOEs of solar electricity due to the higher efficiencies of the more costly premium modules. There are further technology improvements possible down the road, from Perovskite-Si tandem cells with more than 30% efficiency. These technology advancements are still being spearheaded in Europe, paving the way for the worldwide deployment of terawatt-scale PV.
- European policy frameworks for the long-term development of renewables have been created. The European Green Deal and Renovation wave have built the confidence and trust of investors and developers.
- Sustainability, carbon-neutral and eco-design principles together with concrete criteria under consideration have emerged, including recently announced measures to address foreign subsidy distortions in the EU market. These principles became the driving force of the EU's transformation towards green and innovative energy systems and economies. The increasing concern of all customers on CO2 footprint will have structural consequences for the PV manufacturing industry. PV modules produced in Europe using power and resources with favorable CO2 balance and avoiding long-distance transport can show much better eco-design parameters than current Asian products, and this aspect will increase in importance in the coming years.
- A potential competitive advantage for European PV manufacturing has emerged due to new ways to deploy PV in integrated systems. A variety of innovative solutions are being developed and growing rapidly in various sectors including building-integrated PV (BIPV), vehicle integrated PV (VIPV), floating PV (FPV), and agricultural PV (APV). European PV manufacturing companies could benefit from the specific European and local requirements as the integrated systems are more demanding for individually customized solutions.
How much of the solar manufacturing value chain is currently represented in Europe, broken down by segment and capacities? Which areas need to be strengthened?
We don't have numbers for every part of the value chain but these are the general figures in 2020:
- 11% of global PV silicon production: 22.1GW production capacity (Elkem & Wacker)
- 1% of global PV silicon solar wafer production: 1.25GW production capacity (Norsun, Norwegian Crystals & EDF Photowatt)
- 0.4% of global PV silicon cell production: 0.65GW production capacity (Solitek/Valoe, Enel, Ecosolifer)
- 3% of global module production: 6.75GW production capacity (at 29 different companies)
- 25% of inverter production
And this is in a context where Europe installed 15% of all PV capacity in the world in 2020. So, we need to strengthen wafer, cell, and module production if we want to be more self-reliable.
Currently, Europe has a quite severe negative trade deficit when it comes to PV cells and modules. The table below features the total traded value out and into Europe as a region of the international customs category; Photosensitive semiconductor devices, including photovoltaic cells whether assembled in modules or made up into panels; and light-emitting diodes.
2016 [million US$] | 2017 [million US$] | 2018 [million US$] | 2019 [million US$] | 2020 [million US$] | |
European imports | 6 331 | 6 484 | 8 107 | 10 472 | 10 414 |
European exports | 1 701 | 1 645 | 1 721 | 1 565 | 1 767 |
Trade deficit | -4 629 | -4 838 | -6 386 | -8 907 | -8 647 |
What European manufacturing plans will be executed in 2022/2023?
Below are some examples of capacity expansion plans that have officially been communicated. We are aware of some additional large projects, but they have not yet been officially released:
Company | Manufacturing plans |
Meyer Burger | Initiated 400MW of solar cell and module capacity in 2021. By 2022, this should be further expanded to 1.4GW for solar cells and 1 GW for modules. In the long term, production volumes of 5GW per year are targeted. |
Greenland Giga Factory | A 5GW vertically integrated PERC module factory in Seville, southern Spain. Production activities are scheduled to start in December 2023. |
Enel Green Power | Heterojunction solar module factory in southern Italy will be scaled up from 200MW to 3GW by mid-2024. |
MCPV | The Portuguese company is planning a 300 MW fully integrated production line by mid-2022, and in total 15 GW for the future. |
Unigreen Energy | Plans for 1.3GW for n-type wafers, 1GW for solar cells, and around 500MW for PV modules in the Russian exclave of Kaliningrad. Completion is scheduled for March 2023. |
REC | 4 GW HJT module factory in France. The plant is scheduled to start up in 2022, with 2GW produced per year, before reaching its final capacity in 2025. |
Saule Technologies | Inaugurated a perovskite pilot line cell factory in Wrocław, Poland, in 2021, and have started the work to construct an efficient industrial line with a capacity of 100MW. |
Solarge B.V. | A 300MW factory is under development in 2022 in Eindhoven, the Netherlands. |
Kioto Energy | It currently has 150MW of module production, but this capacity will increase to 450MW by the end of the year. Thereafter, there is a goal to add about 300MW of extra capacity every second year. |
Karpat Solar | It has bought equipment from Mondragon and had plans to commission a 100MW module factory by the end of 2021 in Romania |
The EU battery manufacturing industry is kicking off, and one of the goals is to establish a sustainable manufacturing landscape. How is the topic of building a sustainable solar manufacturing base being addressed?
The ESMC has been working on two fronts. Firstly, we have convinced the EU Commission about the need for a new Solar Strategy that addresses the situation of PV manufacturing. Regarding this, the acknowledgment of the need for strategic autonomy and technological sovereignty was completed in May 2021 in the updated EU New Industrial Strategy and accompanying documents by recognizing that building a sizeable EU PV manufacturing industry would also reduce supply disruptions and quality risks.
Secondly, in the summer of 2021, ESMC initiated the IPCEI framework for PV manufacturing in cooperation with the partner organizations of the European Solar Initiative. The PVIPCE initiative is open for all European PV manufacturing industrial partners and research institutes dedicating their efforts to ensure the sustainable competitiveness of European PV manufacturing along all the full value chain.
Fifty members, comprising PV manufacturing companies and research institutes, from 14 European countries have already joined the initiative and work is ongoing in five IPCEI Project Groups.
The PV-IPCEI framework is dedicated to creating the demand for support incentives by securing at least 20GW of sustainably competitive PV manufacturing capacities along the full value chain by 2025 in the EU with a view to scaling it to 100GW by 2030, thus representing at least 15% of the future global market share.
The PV-IPCEI framework and the gigawatt-scale projects are targeted to boost PV manufacturing capacities in the EU by addressing strategic dependency issues and enabling breakthrough research innovations and infrastructure projects through the integrated industrial framework. The circularity of PV production and integrated PV solutions are essential components of the framework to ensure the sustainability and competitive advantage of the European PV upstream sector. Local PV production in Europe could benefit the green transformation and the whole economy as it has lower CO2 emissions and will reduce the import dependency on Asia.
This content is protected by copyright and may not be reused. If you want to cooperate with us and would like to reuse some of our content, please contact: editors@pv-magazine.com.
1 comment
By submitting this form you agree to pv magazine using your data for the purposes of publishing your comment.
Your personal data will only be disclosed or otherwise transmitted to third parties for the purposes of spam filtering or if this is necessary for technical maintenance of the website. Any other transfer to third parties will not take place unless this is justified on the basis of applicable data protection regulations or if pv magazine is legally obliged to do so.
You may revoke this consent at any time with effect for the future, in which case your personal data will be deleted immediately. Otherwise, your data will be deleted if pv magazine has processed your request or the purpose of data storage is fulfilled.
Further information on data privacy can be found in our Data Protection Policy.