Researchers at Germany's Fraunhofer Institute for Solar Energy Systems ISE have developed a busbarless, electrically conductive adhesive-free, and solder-free aluminum interconnection that they claim is a cost-effective and flexible solution for the interconnection of separated cells in shingled solar modules. “We will show a mini-module made with our technology at our Fraunhofer ISE Booth at the upcoming Intersolar in Munich,” the Head of Department Production Technology at the Fraunhofer ISE, Jan Nekarda, told pv magazine.
Conventional processes to connect shingled solar cells usually adopt electrically conductive adhesives (ECAs), with which the rear side busbar of one cell is attached to the front side busbar of an adjacent cell. According to Nekarda, it is still unclear how much cheaper the proposed interconnection technology is when compared to the relevant ECA stringing. “Nevertheless we are confident, that a significant cost reduction will remain, due to the very high silver reduction of our technology,” Nekarda said, noting the Fraunhofer ISE started a cooperation with German PV production equipment provider Manz AG to build a machine for industrial implementation via a publicly funded project.
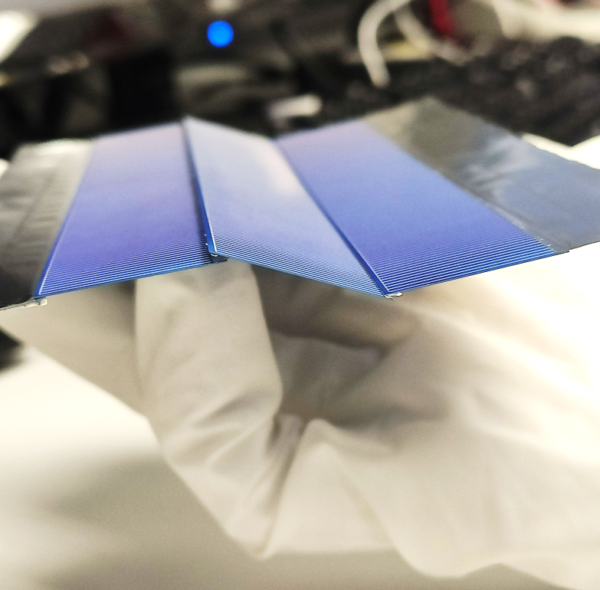
Image: Fraunhofer ISE
Through the proposed approach, ECAs and screen-printed busbars on both sides of the cells are replaced by an 8-μm-thick aluminum foil, called FoilMet. The foil is joined to the silicon nitride (SiNX) passivation via laser metal bond (LMB) process, which the researchers describe as a non-invasive technique that creates bonds between the passivation of the cell and the foil without penetrating the passivation.
“The silver (Ag) fingers and the aluminum (Al) fingers are microwelded to the foil using 300- to 700-μm-long line-shaped joints performed with a single 1-kW infrared continuous-wave laser leaving no necessity for busbar-like structures,” the scientists said. “The simplicity of FoilMet, which connects the fingers of adjacent cells without more intermediate layers than a single Al foil, is of great advantage compared to an ECA interconnection, with joints from the Al finger to the Ag busbar, to the ECA, to the Ag busbar, and to the Ag finger, and therefore consisting of a multitude of layers.”
The German group compared the performance of the novel interconnection technology with that of a conventional interconnection relying on ECAs. The measurements showed that the module fabricated with the foil achieved an efficiency of 21%, while the device without the foil reached 20.3%, with the 0.7% efficiency advantage being attributed mainly due to the increased fill factor. “Regardless of the cause leading to the disparity in the filling factor, in general, good interconnections using ECA can be achieved,” explained the scientists, adding, “FoilMet Interconnect, however, demonstrates the ability to reliably create interconnections with low series resistance and strings with high efficiencies.”
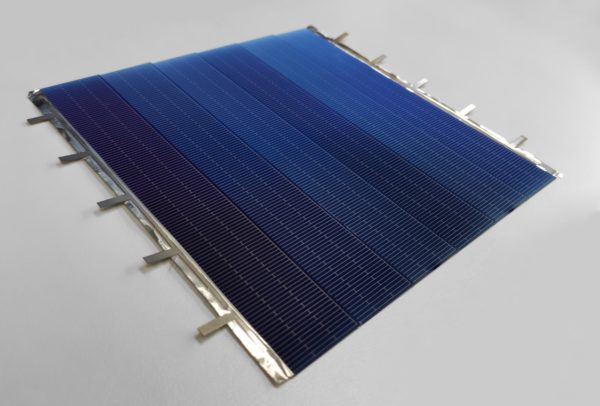
Image: Fraunhofer ISE
They analyzed the performance of the foil in a TC200 aging test to assess the long-term stability of the aluminum interconnection and found that the majority of all shingle strings withstood the stresses of encapsulation.
When asked about the applicability of this new technology in a commercial production line, Nekarda said that unfortunately new processes are never “immediately” applicable to commercial production and need some adaptations. “Compared to other innovations the necessary adaptations seem to be little,” he stated. “The metallization layout has to be changed and the new machine for stringing has to be implemented in the production line. Since new materials are used extensive testing is needed, too.”
The device is described in the paper FoilMet-Interconnect: Busbarless, electrically conductive adhesive-free, and solder-free aluminum interconnection for modules with shingled solar cells, which was recently published in Progress in Photovoltaics.
This content is protected by copyright and may not be reused. If you want to cooperate with us and would like to reuse some of our content, please contact: editors@pv-magazine.com.
7 comments
By submitting this form you agree to pv magazine using your data for the purposes of publishing your comment.
Your personal data will only be disclosed or otherwise transmitted to third parties for the purposes of spam filtering or if this is necessary for technical maintenance of the website. Any other transfer to third parties will not take place unless this is justified on the basis of applicable data protection regulations or if pv magazine is legally obliged to do so.
You may revoke this consent at any time with effect for the future, in which case your personal data will be deleted immediately. Otherwise, your data will be deleted if pv magazine has processed your request or the purpose of data storage is fulfilled.
Further information on data privacy can be found in our Data Protection Policy.