Scientists from the U.S. Department of Energy's National Renewable Energy Laboratory (NREL) have proposed to use silica sands – a stable and inexpensive material with prices ranging from $30 to $50/ton – as a medium to store excess wind and solar power.
The research team developed a thermal energy storage technology called Economic Long-Duration Electricity Storage by Using Low-Cost Thermal Energy Storage and High-Efficiency Power Cycle (ENDURING), which it defines as a scalable solution that can be deployed almost anywhere.
The baseline system, which is designed for a storage capacity of up to 26,000 MWh, works by heating silica particles through an array of electric resistive heating elements at a temperature of around 1,200 degrees Celsius and depositing them on insulated concrete silos for thermal energy storage.
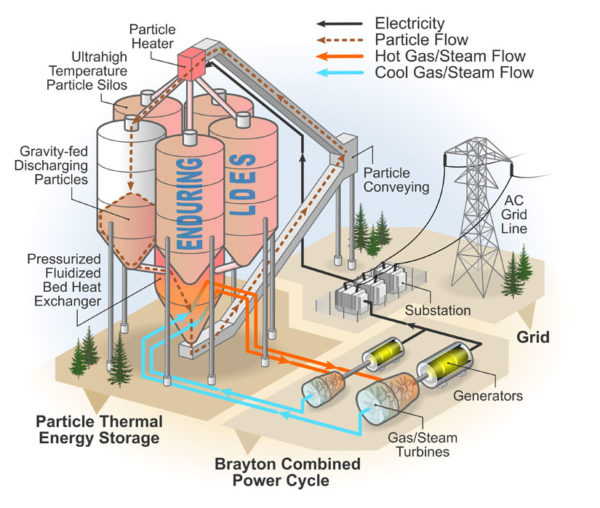
Image: Al Hicks and Besiki Kazaishvili, NREL
“When energy is needed, the hot particles are gravity-fed through a heat exchanger, heating and pressurizing a working gas inside to drive the turbomachinery, and spin generators that create electricity for the grid,” the NREL researchers explained. “Once discharged, the spent, cold particles are once again fed into insulated silos for storage until conditions (and economics) are appropriate again for charging.”
According to them, the proposed storage technology could be deployed at a cost of between $2 and $4 per kWh and it could also be hosted by existing infrastructure from retired coal and gas-fired power plants. Furthermore, it may provide a continuous source of heat for industrial and chemical processes.
“Sand and concrete silos with refractory insulation are very inexpensive materials that can lead to low-cost energy storage,” said NREL researcher Patrick Davenport. “Traditional four-hour storage technologies don't scale well to the grid or city scale. Now that we are in need of large scale energy storage, this technology makes a lot of sense.”
The prototype heaters and heat exchangers for the proposed system are currently being tested under high temperatures.
This content is protected by copyright and may not be reused. If you want to cooperate with us and would like to reuse some of our content, please contact: editors@pv-magazine.com.
The link to the original research is incorrect. What is the power output of the plant? Is it a 1GW plant that can store the energy for a bit more than a day? So it’s cost would be comparable to a nuclear power plant which actually generates power, whereas this just stores power which has to be purchased and there will be maintenance and operating costs as well, like the nuke of course.
This idea would be good for buying up, or actually getting paid to take the negative priced, excess electricity that utilities sometimes have when the wind turbines are generating too much power at night and they don’t want to pay the wind farms to curtail their output.
Crazy days we live in, when the power systems we depend on are designed by idiot politicians taking orders from Big Green insiders.
Hello J. There is no link to the original research in the article.
Typical efficiency of thermal power plants is about 35%, so for 100 mw-hr you put in you get 35 back. Thermal (steam turbine) plants also use a fair amount of water for cooling towers, and have more maintenance costs for pumps and valves.
Es ist mit CO2 ein höherer Wirkungsgrad möglich
As an aid !
https://www.google.com/search?q=ENDURING+energy+storage&client=firefox-b-d&hl=hu&sxsrf=AOaemvJ5h8Fzpu2ndJuBN4EuOcyXrSWc1w:1630561541322&source=lnms&tbm=isch&sa=X&ved=2ahUKEwi4qdGLy9_yAhUO_7sIHbDBDHkQ_AUoAXoECAEQAw&biw=1728&bih=820#imgrc=M06XYwhSedDUrM
The specific heat capcity of silica is around 700 J Kg-1 K-1 while that of water is approximately 6 times higher at 4184 J Kg-1 K-1. Furthermore is silica around 2.5 times heavier than water for a given volume which translates to increased transport costs.
While the silica might be cheap, it is still ‘corrosive’ due to its abrasive nature and will cause wear on mechanical transport systems such as conveyor belts and the like. In contrast, have efficient and application specific water pumps been around for thousands of years in some form of the other.
Silica sand, although not intrinsically toxic, can also cause dust problems through repeated use with negative health effects such as silicosis and is a factor to be reckoned with. On the other hand does water not degrade every time it is pumped around the system and a UV steriliser and basic filter system should be enough to maintain the water quality.
The only possible downside to water is the evaporation which will take place, but (hot) water storage systems have also been around for a long time with technical problems been address fairly succesfully.
Wouldn’t it be easier and more effective to use the proposed setup and store excess energy in water that is relatively abundant?
specific heat capacity of water may be 6 times higher per K, but water can’t be heated to 1200 degrees Celsius. So it really doesn’t matter water has higher thermal capacity.
CO2 ist wirksamer.
https://edison.media/energie/energy-dome-speichert-strom-mit-kohlendioxid/25219528/
The NREL press release uses a lot of words, but does not say what the planned secondary working fluid might be. Other high-temperature generating schemes have proposed closed-circuit carbon dioxide,
Gert Benade; isn’t phase change a problem with water? To keep it liquid at 1000 deg C, you need very high and quite risky pressures. Sand stays sand, and needs no pressurisation.
This technology should be used to store process heat. Process heat demands in the United States are upwards of 3000 to 4000 TWh which puts this end use on par with end-use electricity demand.
Using these sorts of systems to provide process heat would allow you to achieve far higher capacity factors than using them to provide grid electricity. If this system was primarily dedicated to supplying process heat this would tend to subsidized the thermal storage costs such that it may be economical to use these system to provide grid electricity. You could imaging using this stored thermal energy to supply the steam portion of a NGCC plant. If this storage tech was only used to provide electricity the economics you’d have a much harder time making the economics pencil. I haven’t modeled this type of system at $2/kWh but I have modeled it at $5/kWh and the economics weren’t even close. When you subsidize and/or blend down the thermal storage costs by using the system for process heat the economics are far more favorable.
As a side note, you would never want to couple this system to an expensive Brayton cycle. This is a situation where the fuel is cheap so you’d tend to prefer an cheap off the shelf power train.
I have reconsidered my initial statement of storing heat in water and have to agree with James Wimberley that phase change is a dangerous and challenging issue.
And, as Lee Kasten points out, should this technology probably be used as a direct storage for process heat rather than trying to convert heat back into electricity as this process is not entirely efficient.
Unfortunately does the NREL press release not give enough technical details, but I suppose that any advances on energy storage is a step in the right direction.
The proposed process, with the exception of the heating and heat exchange method, is similar to a refinery FCC (fluidized bed catalytic cracker) with a power recovery turbine added to recover waste heat and pressure. The FCC process operates at 2 to 4 bar gauge and 850 C. Air is injected into the FCC process using an axial compressor providing combustion air to burn coke / carbon off the circulating aluminum oxide and silicon oxide catalyst particles that range up to 150 microns in size. Catalyst is separated from the combustion products through several stages of cyclones and the gas then flows through the power recovery turbine. FCC power recovery turbine designs are specialized designs because it is impossible to remove all the particles from the gas stream so the turbine flow path is subject to erosion. Particle separation and removal in the cyclone stages is critical to turbine reliability.
The proposed process heats the storage medium, silica sand, using excess electricity from solar, wind, or other low or no carbon generation sources. The FCC process combustion side design including the regenerator (combustion) vessel, cyclone separator, vessels, and piping could be readily adapted to the proposed process design. All of the technology exists and while not “off-the-shelf” the design factors are well known. Stretching the design to 1000 C would require upgrades across the board in the components to more costly grades of materials than used in today’s modern refinery FCC processes.