From pv magazine Spain.
In some PV markets, projects are getting older and certain owners and operators are beginning to rethink their asset management strategy. The choice is clear: maintain the asset on the basis of preventive and corrective maintenance, determined by the original electromechanical condition; or invest in new equipment to extend the life of the asset, assuming the challenges that entails. In this, three-part article, Asier Ukar, senior consultant at PI Berlin and general manager of the German engineering company’s Spanish subsidiary, will address several issues that will allow us to understand the benefits of revamping without losing sight of the challenges and risks involved in carrying it out on a photovoltaic asset.
This first installment of the interview investigates the scenarios that justify revamping, or plant modernization strategy. The first question that naturally comes to mind is, in which scenarios does revamping make sense? PI Berlin identifies four: when there is a big technological leap between the grid connection date and the revamping date; when plant performance is compromised due to poor execution practices and there is an electricity tariff or feed-in-tariff (FIT) in force; when the natural aging of the plant requires it; and when an IPP (independent power producer) wants to homogenize its portfolio, made up of assets built in different periods and made up of technologies of different natures. Let's analyze them one by one.
Scenario 1: The original technology no longer exists
This could mean a scenario in which there has been a big technological leap between the original date of connection and the date of revamping. Take Spain or Italy as an example. These markets experienced big expansions between 2006 and 2008 and between 2009 and 2011. At that time, it was common to build PV plants using solutions that are practically extinct today, such as dual-axis trackers, 60-cell crystalline PV modules (measuring 1,650x990mm), galvanically separated inverters, thin film amorphous silicon, or CIGS module technology.
In addition to purely technical factors, there are also economic factors that have influenced the development and implementation of PV installations. For example, the Spanish regulatory framework that led to the division of PV plants into 100 kW islands with individual transformers and meters, or the strong demand for modules caused by Italy and Spain that forced many installers to purchase, for a single plant of a few megawatts' capacity, modules from various manufacturers and technologies in order to meet the required volume. The technical characteristics of the PV components available between 2006 and 2011, as well as economic and regulatory factors, were characteristic of the nature of the first PV plants. Progress on technology and policies means these strategies have now practically disappeared.
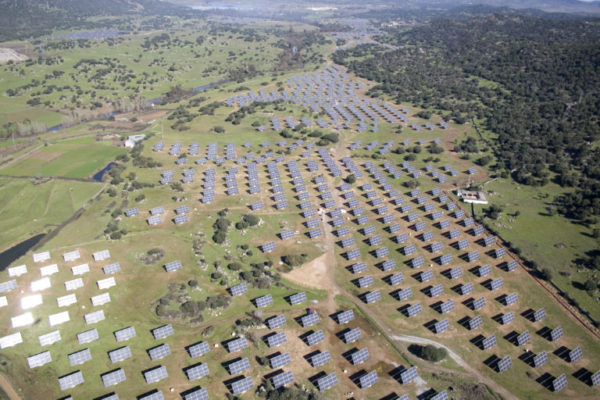
Image: PI Berlin
Scenario 2: There is a FIT, but the plant is under-performing
Since FITs typically guarantee a price per kilowatt-hour generated within predefined limits and under-performance can quickly become a serious problem for project economics.
Under-performance can be due to many factors, including poor installation practice, product failure, or a combination of the two. Ukar lists several examples to illustrate these aspects, such as (i) flimsy design of dual-axis trackers; (ii) trackers based on prisms rather than astronomical tracking, adding complexity and wear on moving elements; (iii) use of three-pole AC cables for DC applications; (iv) reduced cable capacity due to excessive accumulation of cables in trenches or troughs; (v) mistreatment of modules on-site, with consequent damage to cells or glass and back foil; (vi) very permissive engineering, procurement and construction (EPC) contracts that barely contain requirements for quality control during construction and commissioning; (vii) the absence of a SCADA system that would allow adequate monitoring of plant operation and failures; (viii) a lack of knowledge of degradation phenomena such as PID; and (ix) lack of quality control during PV module manufacturing. “In some plants installed in Spain or Italy before 2011, it is not uncommon to find disoriented or stopped trackers, incorrectly labeled modules, detached diode boxes, inverters with poor grid synchronization, or plants where the performance ratio is not monitored at all,” Ukar said.
Failures can be partly justified by the rush some installers and developers had to deal with due to tight construction schedules and short supply of modules, and also from a lack of experience in the sector. In any case, there are, today, a large number of PV plants operating well below their theoretical yields, leading not only to wastage of the tariff, as mentioned above but also, in the specific case of Spain, the risk of the loss of the tariff entirely for not reaching the minimum threshold of operating hours.
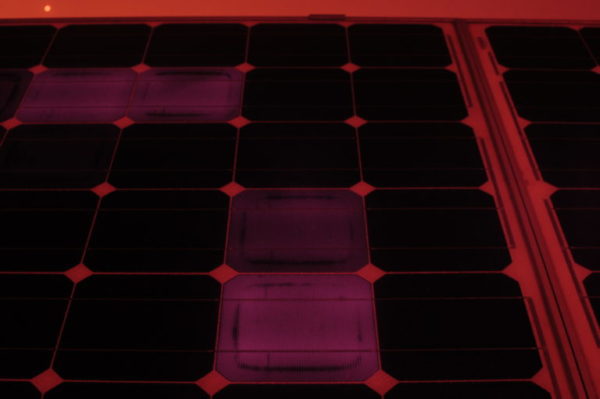
Image: PI Berlin
Scenario 3: Plants at the end of their useful life
Here we consider ‘natural’ aging of the plant by itself as an argument to justify revamping, regardless of under-performance or construction defects.
This will focus mainly on modules and inverters, since these components have been most thoroughly studied in relation to their lifetime. The 10 to 12-year threshold is commonly considered the point at which replacement of the most sensitive inverter components (mainly IGBTs, capacitors and filters) will be required. In the case of string inverters, this means almost a complete replacement of the inverter, while in the case of central inverters it would mean the replacement of these parts while maintaining more durable components, such as busbars, racks or certain protections. High temperatures and high DC/AC ratios undoubtedly shorten inverter lifetimes. Therefore, greater longevity is expected in central European climates compared to tropical climates, where humidity should also be added as a degrading factor.
As for PV modules, different degradation trends are observed depending on the technology used and location. These differences can be seen in established markets such as Germany, Italy or Spain, which have a large number of PV plants that have entered the last third of their useful life. It should be noted the environmental factors that first trigger degradation effects are high temperatures and high exposure to UV radiation, or a combination of both. This phenomenon is clearly observed in modules installed on dual-axis trackers, which are widely present in both Italy and Spain.
In these cases, modules are subjected to high temperatures and high radiation for long periods due to the theoretical perpendicularity that the tracker seeks with respect to the incident radiation. This is why phenomena such as yellowing, corrosion of busbars, chalking or degradation of cables and connectors are frequent in these plants, and somewhat less frequently observed in countries such as Germany, where the use of two-axis trackers is restricted mainly to the south, and where environmental conditions are benevolent for PV components.
India
Adding India as a fourth market with around ten years of accumulated lifetime in a significant number of plants, we observe that the levels of decay described above emerge in a significantly shorter time, as a result of the confluence of environmental stress factors such as high humidity, high temperatures, salinity or high UV radiation. In states including Rajasthan, Gujarat or Tamil Nadu, it is not uncommon to find signs of accelerated aging in modules, electrical panels or inverters with associated insulation problems, overheating due to dust accumulation, corrosion in wiring, or cracking of the backsheet.
It should not be forgotten that product warranties provided by module manufacturers in the early days of PV rarely exceeded five years, and that the only certifications required in more than 90% of cases were restricted to IEC 61215 and IEC 61730 – both necessary but clearly insufficient to predict the performance of a module beyond the first few years of its life. As in the second scenario described above, a low performance ratio – for whatever reason – is a waste of the tariff and therefore a loss of return.
The rate of aging for modules and other components depends on the number of environmental stress factors that converge simultaneously. The incidence of these factors is different in Southern Italy than in Germany, as well as in the case of fixed-tilt or dual-axis tracking. Most of the defects associated with such aging are not covered by the expired product warranty, which is particularly relevant in the case of modules installed more than a decade ago whose product warranty was generally limited to five years, as opposed to today's 12 years or more.
Scenario 4: Portfolio clean up
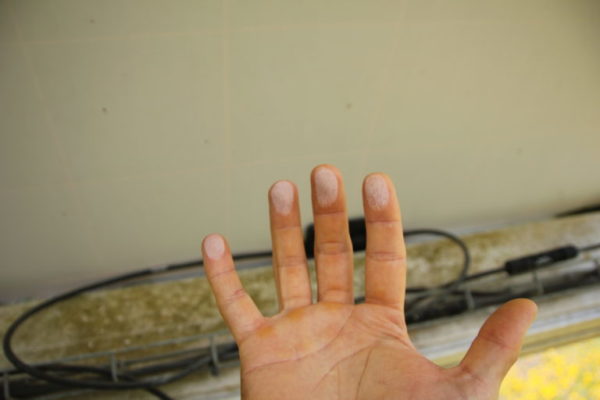
Image: PI Berlin
In this scenario, revamping is considered by an independent power producer looking to homogenize a portfolio that is made up of assets acquired at different times, and therefore made of different technologies. We are talking about portfolios of multiple plants, most of them less than 3 MW, and installed with varying technologies such as low-power crystalline modules; thin-film modules which are now practically extinct, such as amorphous silicon or CIGS; old inverters with low efficiencies; dual-axis trackers with prism tracking etc.
Such asset collections involve the management of plants of very different sizes and technologies, which undoubtedly adds complexity and increases operation and maintenance (O&M) costs due to the different requirements of each plant and the impossibility of implementing standardized maintenance which could benefit from an economy of scale.
The confluence of one or more of the scenarios described above in a single plant, which is very common, justifies revamping from a cost-benefit point of view. First, by an increase in the efficiency of the components with a direct influence on the performance ratio (especially modules and inverters); secondly, by the possibility of correcting installation faults with a direct impact on electrical safety and loss of energy yield; thirdly, by the possibility of reducing O&M costs through standardization and the smaller number of elements in operation; and finally, by the added remuneration thanks to the extension of the plant's useful life.
Parts two and three of this article will follow next week.
This content is protected by copyright and may not be reused. If you want to cooperate with us and would like to reuse some of our content, please contact: editors@pv-magazine.com.
1 comment
By submitting this form you agree to pv magazine using your data for the purposes of publishing your comment.
Your personal data will only be disclosed or otherwise transmitted to third parties for the purposes of spam filtering or if this is necessary for technical maintenance of the website. Any other transfer to third parties will not take place unless this is justified on the basis of applicable data protection regulations or if pv magazine is legally obliged to do so.
You may revoke this consent at any time with effect for the future, in which case your personal data will be deleted immediately. Otherwise, your data will be deleted if pv magazine has processed your request or the purpose of data storage is fulfilled.
Further information on data privacy can be found in our Data Protection Policy.