As the July edition of pv magazine has illustrated, work on integrating circularity into the PV and energy storage industries is ramping up. In Europe, for example, there are currently three projects under way – the Circusol, Cabriss and Super PV initiatives – under the aegis of the European Commission’s Horizon 2020 research program.
European solar panel manufacturer Solitek, which recently received silver-level Cradle-to-Cradle certification for its modules, is involved in all three of those EU initiatives. Project manager Tadas Radavičius spoke to pv magazine as part of our UP quarterly theme on circular manufacturing.
pv magazine: What is the ‘Super PV’ project and how did you become involved in it?
Tadas Radavičius: After successful participation in the [Horizon 2020-backed] Cabriss project [for the implementation of a circular economy based on recycled, reused and recovered indium, silicon and silver materials for PV and other applications], where Solitek was involved in activities like the recycling and reuse of materials for PV cells and modules, we were invited to continue working on circularity in the PV sector in another project: Super PV.
The goal of the Super PV project, which has an overall budget of €11.6 million, is to lower the levelized cost of energy of a solar system by between 26% and 37% via innovations in PV modules, solar system design and electronics. Currently, we have tested various innovations in-lab and are moving towards the demonstration of these innovations in desert, tropical, and cold climates.
Circular manufacturing
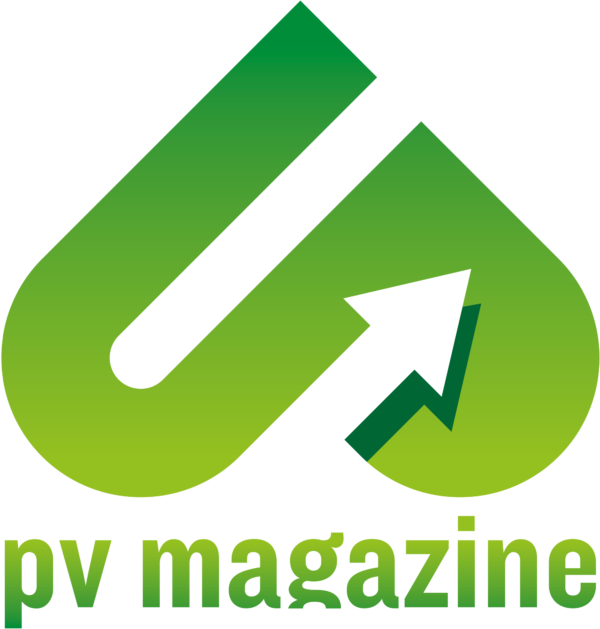
Can you provide some examples?
We are working on three types of innovation:
- Introducing and combining five PV module innovations applied to c-Si-based bifacial and to CIGS modules.
- Module-level power electronics developments to ensure higher power output, performance monitoring and data collection at a string level, and long term stability of operation.
- PV system integration and process innovation, developing a new digital and holistic process: PIM [PV information modelling/management].
One of the PV module-level innovations is nano-coatings which can have anti-soiling, easy-to-clean and anti-reflective properties. Other innovations are in-laminated diodes and light-harvesting. These innovations are already showing promising results after the first tests.
It is the second year of the Super PV project, out of a total of four years. Results from power electronics and PV system integration and process innovation will be seen in demonstrations.
You have also been working closely with the Circusol consortium. What have you been doing there?
Solitek is providing input to Circusol from the perspective of a solar panel manufacturer. We are involved in the co-creation of circular business models for second-life solar panels and refurbished EV batteries.
Another part of our research focuses on the digitization of the PV industry by using RFID [radio-frequency identification tag] technology. This technology allows attaching in-laminate tags for each panel. The tag can contain, in itself, information that would be useful for installers and recycling companies, such as technical parameters and material composition. Another option RFID unlocks, is the creation of databases where RFID tags could contain URL links. This would [enable] an online database of each panel or PV system. Manufacturers, installers, recycling companies and researchers could benefit from this information. Feasibility and the costs [and] benefits of creating such a database through RFID, QR [quick response, bar] codes, relying purely on software solutions and so on, will be assessed.
We are also responsible for investigating alternative materials for solar panels, to reduce toxic constituents and make the panel better designed for recycling. One of the current research topics is the use of lead-free ribbons, where lead is replaced by bismuth.
One study by the Fraunhofer research institute into life cycle assessments, concluded bismuth is no more sustainable than lead. What makes you think it is an effective replacement?
Currently, we are seeing theoretical obstacles towards recycling ribbons which have bismuth, such as weaker ribbon performance compared to lead ribbons. Sustainability is also an issue. As bismuth is a by-product from lead production, it does not make it such a green alternative. Tests are ongoing, however we do not see a ribbon alloy with bismuth as an effective replacement at the moment. We are looking for other types of lead-free ribbons as possible replacements.
What business models do you see as being most effective for a circular module manufacturer, and why?
With policies currently being shaped, like … eco-design and energy labelling, the solar industry will become more transparent. There will be increasing incentives for manufacturers to aim for higher standards by, for example, declaring their material content, and information about recyclability, manufacturing and organizational processes etc. This will promote businesses who are including circular economy principles, such as responsible end-of-phase components handling, reducing toxic materials within the panel, long durability of solar panels, using renewables in manufacturing facilities etc.
There are two solar panel manufacturers in Europe – [Chinese state-owned] REC Group and AE solar – which recently integrated NFC [near-field communication] and barcodes into their panels so installers can use their phones to scan them and final users can access relevant information. These are examples that competition is increasing not only through providing high-efficiency panels, but also through sustainability and digitalization.
What work has been done on redesigning modules to include circular-economy principles? How different is such a design from today’s modules? What stage are you at in this project? What are the costs versus traditional modules?
So far, our research covers fluorine-free backsheets, lead-free ribbons and integrating a unique identification – RFID, QR code, barcode etc – into each panel to access and/or add information about the products. The aim for this design is to create a panel which could be utilized successfully for [the] second-hand panel market and for easier monitoring and maintenance. Currently, each panel has [a] barcode and number on it which can be traced back to the manufacturer. Sometimes information about testing results can be accessed if the customer sends the barcode to the manufacturer for them to check their internal database. What we envision is simpler and [more] flexible approaches to accessing and adding additional information about each panel.
For our particular task in the Circusol project, we produced two batches of mini-modules with lead-free ribbons, fluorine-free backsheets and various RFID, UHF [ultra-high frequency] and NFC tags. These mini-modules are undergoing climate chamber tests and the RFID functions will be tested by installers. Eventually a comparison will be made in recycling the parts, compared to normal panels. All these materials increase the costs of solar panels. For RFID tags, for example, prices vary from €0.10 to €1, depending on quantity and type of tag.
What do you see as the main barriers and opportunities for the adoption of circular solar principles?
Due to the lack of end-of-life [use], solar panel recycling is usually still not economically feasible. Moreover, the development of recycling technologies is still immature and ongoing. These are the main barriers for the proper recycling of solar panels and the recovery of high-purity materials.
Another barrier for bringing back solar panels for second-use, is expenses … from de-mounting solar systems, inspecting them and re-installing them. Also, the higher the age of solar panels, the less efficient they are compared to new ones. It is also difficult to locate solar panels that are being removed and discarded, even though they are still capable of producing electricity.
One of the main opportunities is switching to ‘servitization’ – also known as “product-service system” – business models. It is one of the circularity principles which underlines the importance of [the] professional maintenance of products and their proper handling through re-use, repair and recycling. This is [made] possible by keeping the ownership of the product – in this case the solar PV system – for a company, [whether a] producer, installer or independent service provider. The service provider has a strong motivation to make sure the solar PV system works well throughout its lifetime in order to ensure a recurrent revenue stream from the customers.
This content is protected by copyright and may not be reused. If you want to cooperate with us and would like to reuse some of our content, please contact: editors@pv-magazine.com.
By submitting this form you agree to pv magazine using your data for the purposes of publishing your comment.
Your personal data will only be disclosed or otherwise transmitted to third parties for the purposes of spam filtering or if this is necessary for technical maintenance of the website. Any other transfer to third parties will not take place unless this is justified on the basis of applicable data protection regulations or if pv magazine is legally obliged to do so.
You may revoke this consent at any time with effect for the future, in which case your personal data will be deleted immediately. Otherwise, your data will be deleted if pv magazine has processed your request or the purpose of data storage is fulfilled.
Further information on data privacy can be found in our Data Protection Policy.