Researchers at Scotland’s Heriot-Watt University have developed a waterless self-cleaning technology for PV panels which involves vibration to remove dust and sand by exciting fundamental frequencies in the modules.
“It is not the first system based on a vibration mechanism but it is the first inspired by cymatics,” said research coordinator Edwin Babu, referring to the study of sound vibration to understand the nature of sound and matter – or, in more recognizable terms, the characters of the Big Bang Theory TV show putting a cornstarch mixture on an amplifier and watching the patterns.
The Heriot-Watt process operates at a lower frequency than the 20kHz or higher band at which ultrasonic cleaning systems typically run.
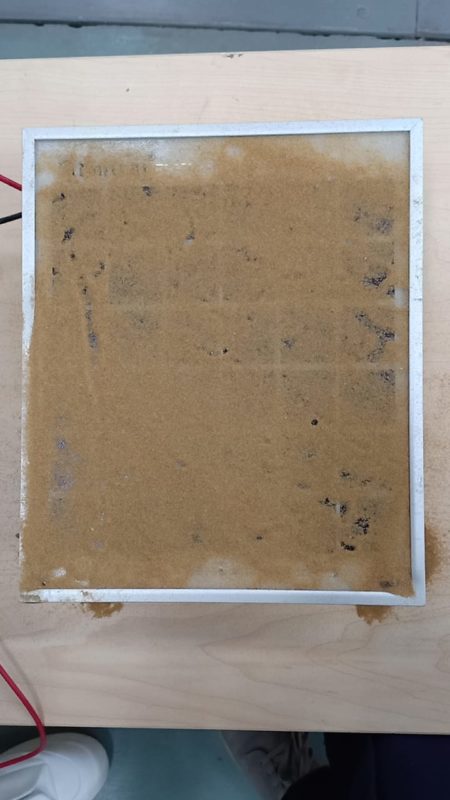
Image: Heriot Watt University
The researchers investigated the structural integrity of module laminate from the frequency response of vibration sand, and the mechanical stresses within critical layers of the laminate using the finite element method commonly used in engineering and mathematical modeling.
DC motor
The self-cleaning mechanism involves attaching a DC motor to the backsheet of a panel. A solar module was supported on four edges to emulate a system being excited by an unbalanced mass to induce vibrations, the researchers said, adding: “The set-up was arranged to be constrained firmly and allow vertical vibrations throughout the laminate.”
When the rotor from the eccentric mass DC motor reached the rotational speed of the first natural frequency, a large amplitude of vibrations was induced on the panel. The intensity of the amplitude, the researchers said, could be controlled by the damping ratio of the system – the ability of the structure to dissipate the energy caused by vibrations.
Mechanical stress
The Heriot-Watt researchers said they still need to confirm the limit to which laminate can be exposed to such vibration before suffering excessive mechanical stress and possible failure.
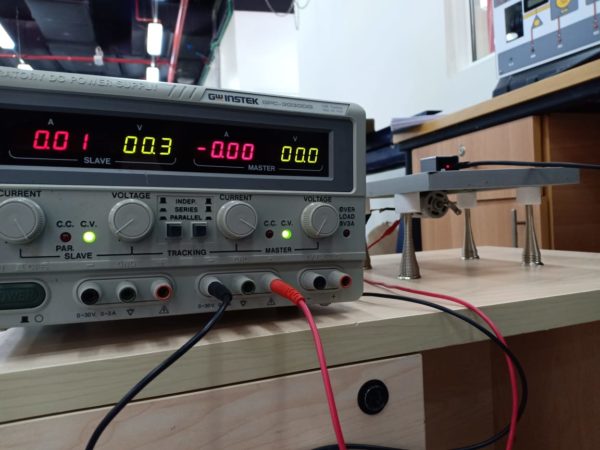
Image: Heriot Watt University
“The mechanical stresses induced [are] yet to be tested since a mutual ground for comparing parameters [needs] to be obtained, which can be done in the near future,” said Babu. “Tests are being conducted for the silicon cell and glass layers using computational simulation and [a] limit was found which was within the safe region of developing micro-fractures. We found that this could vary [depending] on the panel size.”
Thus far, testing has been carried out on a small panel, to observe the effect of the vibration on each layer of the laminate.
“The current challenge is to find the sweet spot, in terms of frequency and amplitude, and make the vibration … effectively clean the surface,” said the research coordinator. Babu said the process offers very efficient behavior which can be tuned for cleaning purposes.
The process is described in the paper Cymatics Inspired Self-Cleaning Mechanism for Solar Panels, which is under review for publication in the Journal of Cleaner Production.
This content is protected by copyright and may not be reused. If you want to cooperate with us and would like to reuse some of our content, please contact: editors@pv-magazine.com.
I wondered why this has not been developed yet. This method is already used in photography machines where the small internal CCD/CMOS glass is cleaned by ultrasonic vibration, were all dirt and dust is removed in that way. This was developed by Canon and used in all their EOS Cameras for a long time. Now the question is if the panel structure and sandwiched layers can sustain such vibrations in the long term. As somebody says, this is a story under development.
I have installed 1kw solar power plant on my rooftop have to wash it biweekly for better results,but if it is a big project then this new technology will be helpful….
Seems doable , this is what came to my mind when I think of cleaning I could only think of vibration or compressed air purging but the latter is not energy efficient as such. Thanks for sharing this report