The Fraunhofer Institute for Solar Energy Systems (ISE) has joined forces with the Photovoltaic Technology Evaluation Center to improve the screen-printing process used to apply silver fingers in silicon solar cells.
The fine-line metallization process tested in southern German labs allows for a less-than-podgy finger width of 19µm and height of 18µm in a single printing step, compared to the current 30µm. The researchers claim their innovation could reduce module silver consumption 30%, a figure which would have significant ramifications on overall manufacturing costs.
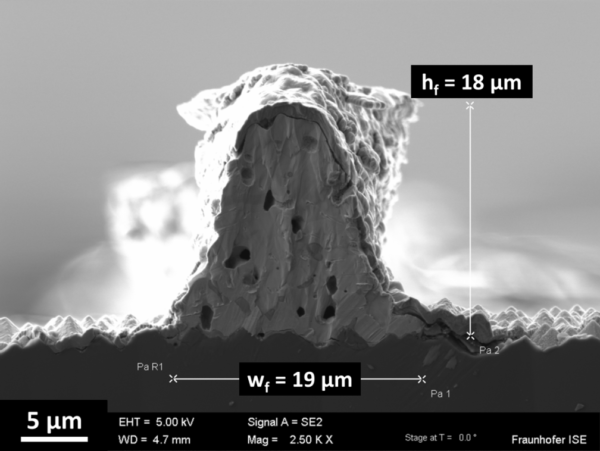
Image: Fraunhofer ISE
“Working together with industry partners in fine-line screen printing metallization – in particular with screen manufacturers Koenen GmbH and Murakami Co Ltd, as well as screen chemical supplier Kissel + Wolf GmbH – we have managed to reduce the contact fingers’ width to less than 20 micrometres, a reduction of 30-40% compared with the current industry standard,” said Andreas Lorenz, project manager in the printing technology group at Fraunhofer ISE.
Slimmer fingers not only reduce silver content but prompt improved electrical properties, the team stated. When new printing technology is used with more modern 8-15 busbar technology, there are notable reductions in power losses in the contact fingers.
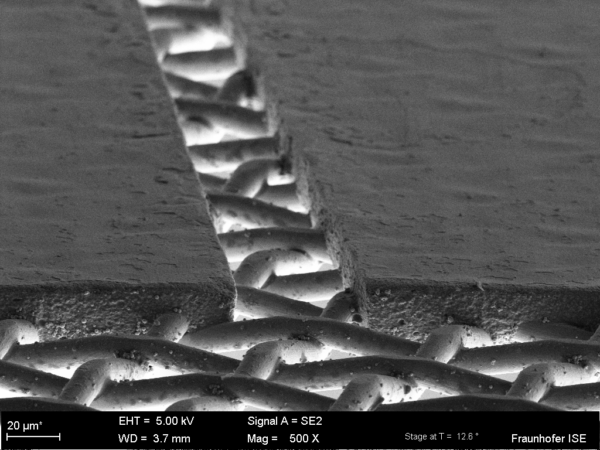
Image: Fraunhofer ISE/ Koenen GmbH
The team also used a new fine-mesh screen for the metallization process of passivated emitter rear contact (PERC) solar cells in two independent series. For the PERC experiment, Fraunhofer ISE used optimal screen parameters, and “a nominal finger width of 24µm due to the limitation concerning the available number of busbars on the solar cell (in this case five)”. The institute claimed the best performing PERC cell in the experiment had a conversion efficiency of 22.1%.
“Using highly engineered screen and paste systems for fine-line metallization it could be possible to start manufacturing solar cells with nearly invisible contact fingers on an industrial scale in the near future,” said Florian Clement, head of production technology at the institute’s structuring and metallization department. “This would represent a great advantage for applications in integrated photovoltaics, where aesthetic, homogeneous module surfaces are in demand.”
The amount of silver needed to produce conductive silver paste for the front and rear of most PV cells could be almost halved by 2028, from an average of 130mg per cell in 2016 to approximately 65mg, according to the Role of Silver in the Green Revolution report published by CRU Consulting on behalf of The Silver Institute.
Silver demand
The report’s authors explained the amount of silver used in solar cell manufacturing had already decreased from 400 to 130mg between 2007 and 2016. The authors predicted cell output would grow from 4.7 W now to 6 W by 2030, contributing to a 10.5mg reduction in silver use per watt.
The need to cut down silver use was illustrated by the findings of the World Silver Survey 2019 report published by The Silver Institute. According to the survey, silver prices grew 7% last year after rising 4% in 2017. That trend, according to the institute, was down to record demand growth in the PV industry.
The Fraunhofer ISE metallization project was funded by the German Federal Ministry for Economic Affairs and Energy. More detailed results of the research collaboration with Koenen, Kissel + Wolf and Wickon Hightech GmbH, have been promised at the EU PVSEC show in Marseille next week, and at PVSEC in Xi’an, China at the beginning of November.
This content is protected by copyright and may not be reused. If you want to cooperate with us and would like to reuse some of our content, please contact: editors@pv-magazine.com.
1 comment
By submitting this form you agree to pv magazine using your data for the purposes of publishing your comment.
Your personal data will only be disclosed or otherwise transmitted to third parties for the purposes of spam filtering or if this is necessary for technical maintenance of the website. Any other transfer to third parties will not take place unless this is justified on the basis of applicable data protection regulations or if pv magazine is legally obliged to do so.
You may revoke this consent at any time with effect for the future, in which case your personal data will be deleted immediately. Otherwise, your data will be deleted if pv magazine has processed your request or the purpose of data storage is fulfilled.
Further information on data privacy can be found in our Data Protection Policy.