The humble solar cell has come a long way in ten years, and in some ways it appears the pace of change is accelerating. However, solar manufacturers remain conservative when it comes to new technologies and incremental rather than step changes are still the norm. Incremental can still be powerful, though, particularly when executed at scale.
Efficiency and power output continues to climb
Ever increasing module and cell efficiency increases were on display at SNEC this year. Gone are the days when landmarks such as a 400 Wp module or 20% efficient PERC – passivated emitter rear contact – cell were thought to be the final word. The latest improvements appear to be occurring at a more rapid pace than previously, with large scale transitions to high efficiency cell concepts and the adoption of new module technologies being deployed almost overnight.
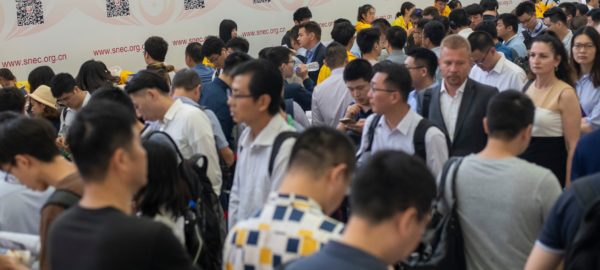
Image: pv magazine/Dave Tacon
The momentum behind mono PERC was clear at SNEC. Some of the efficiency achievements achieved using mono PERC – coupled with a selective emitter – were outstanding. Producers such as Risen are pursuing a roadmap of cell efficiencies north of 22.5% on p-type mono PERC technology. On the module front, paved approaches – where half cut cells very slightly overlap vertically – were deployed. The paved technique goes by various names including tiled or gapless. Visitors also saw the cell interconnection technique seamless soldering, which requires more flexible interconnection ribbons and a few stringer providers can provide automated equipment. The upside could be considerable, with module makers claiming it could push large format module output to 500 W.
Looking ahead, some SNEC visitors predicted the current cell and module efficiency improvement roadmaps could prove too conservative. Some believe 500 Wp modules from mainstream manufacturers could be presented as early as next year, with larger wafers and form a factor. In cell terms, 25% conversion efficiency may not be too far away. For cell efficiencies to hit that milestone new technologies will be required, with PERC having reached its fundamental limit. By comparison, the 10th International Technology Roadmap for Photovoltaic report published by the German Mechanical Engineering Industry Association expects 144-half-cell modules to hit 420 Wp for mono PERC by 2029.
Mono PERC, n-type TOPCon, HJT and perhaps perovskite
Solar cell technology roadmaps among major manufacturers continue to embody evolution rather than revolution although there are signs that could be changing. PERC upgrades of cell lines continue to be made, with mono PERC absolutely mainstream.
The next step for production lines appears to be a switch to n-type and TOPCon – tunnel oxide passivated carrier-selective contacts – in particular. The upgrade of a p-type PERC cell line to n-type TOPCon is no small challenge, however the expense is not prohibitive according to some manufacturers. It is worth noting, though, that at this stage of its development, some TOPCon lines are not delivering such a significant efficiency increase on PERC – particularly when cells are incorporated into a module. For example, Trina Solar displayed modules deploying mono PERC and TOPCon side-by-side at the 2019 SNEC, with module efficiencies of 20.4% and 20.7%, respectively.
For new cell lines there seems to be genuine appetite for heterojunction (HJT) technology, with manufacturers either running pilot lines or announcing significant HJT expansion plans. Tongwei reported it will start production on a 400 MW heterojunction line in July, with plans to expand to 1 GW next year. Risen plans to build a 2.5 GW heterojunction fab with the first 500 MW of equipment in place by late next year.
And there appears considerable potential for HJT to deliver a major lift in efficiencies. Singaporean manufacturer REC unveiled its Alpha HJT module line at Intersolar last month. The HJT equipment supplier is Meyer Burger and during SNEC the Swiss toolmaker said with experienced cell engineers running the HJT line in full production, major efficiency gains above initial results of around 22.4% at module level, were to be expected – that 25% cell efficiency milestone may be in sight.
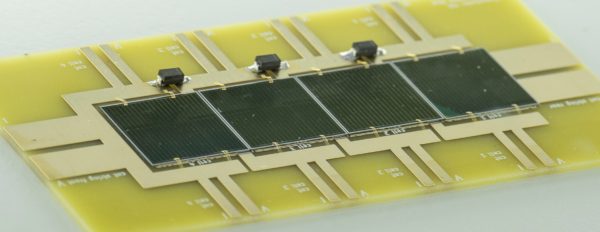
Image: pv magazine/Dave Tacon
Looking further ahead, perovskites and tandem cells were widely discussed during SNEC and displayed by a handful of manufacturers and equipment providers. Germany’s Centrotherm featured a III-V-Tandem mini module produced by scientists at Fraunhofer ISE at its booth, demonstrating “the next step” to high efficiencies after HJT. The Oxford PV team were present and chief technology officer Chris Case delivered a much talked about presentation about the LCOE (levelized cost of electricity) potential of high efficiency tandem perovskite-HJT cells. Not to be left behind, Chinese companies are also active in the technology. Cell maker Tongwei is part way through a three-year research and commercialization project and displayed a perovskite cell at its booth. Homegrown perovskite startups such as Hangzhou Microquanta are also pursuing the technology.
Wafers go big and mono-like
One apparently simple way to boost efficiencies, particularly on a module level, is to increase the size of PV wafers. While gradual moves to increase wafer sizes have been mooted for some time, Longi is spearheading 166mm wafers in an effort to make them the new standard. The mono giant is not alone, with Jinko having deployed larger wafers in its Swan series.
Challenges remain for larger wafers, particularly when incorporated into necessarily larger modules. Changing the form factor of the module may make them unsuitable for re-powering projects or some commercial and industrial rooftop designs.
With mono continuing to demonstrate superior competitiveness over multicrystalline PV, what will manufacturers do with their many tens of GW of multicrystalline production capacity? A potential answer came in the form of cast mono, also known as mono-like or quasi-mono. While the technology has been around for some time, it appears numerous ingot and wafer producers are doubling down on efforts to increase mono-like yield. Unlike mono, only part of the cast ingot is of a monocrystalline structure and performance. The best way to deal with the outer sections of the ingot, likely low-quality multicrystalline, remains an open question.
Intellectual property matters
It was only one or two years ago that shingled module technology was cutting edge, because it reduced dead module space, maximizing output. Shingled modules were less prevalent this year, however, with visitors attributing the shift to IP concerns. Representatives of SunPower – which has demonstrated its willingness to aggressively safeguard its shingling IP – were in attendance in Shanghai as the company looks to scale up its made-in-China Maxeon module series.
In some circles China has been depicted the Wild West when it comes to solar technology IP. Critics have alleged copycat products have popped up across the Chinese supply chain and, if that were the case, why are IP concerns only surfacing now?
There could be two dynamics at play. First, the Chinese domestic market has become increasingly uncertain in the face of regulatory changes, necessitating Chinese suppliers to look overseas for buyers – to markets where they will encounter IP claims. The second is the Hanwha Q Cells PERC lawsuits, launched in parts of Europe, the U.S and Australia. It may well be the case that this major piece of legal action, which affects some Chinese suppliers, could have sharpened the industry’s focus on IP.
Increasing consolidation
While it is far from the case that China’s PV industry is struggling, there are signs long anticipated consolidation is gathering momentum. Interestingly, it appears set to affect not only Tier 2 or 3 businesses but also major players, although potential Tier 1 exits, acquisitions or mergers are being discussed as rumors at this stage rather than official announcements. pv magazine will be following up on those leads in the weeks ahead.
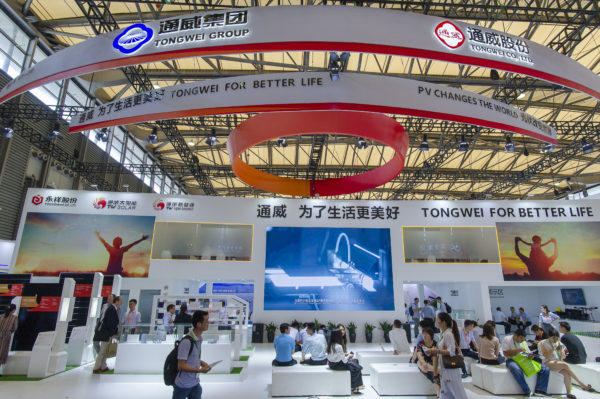
Image: pv magazine/Dave Tacon
Alongside such informal rumors there were also significant supply deals and transactions announced during SNEC. A majority stake in GCL New Energy Holding was sold to China Huaneng Group, one of China’s largest state-owned energy groups. GCL also announced 6 GW worth of mono wafer supply contracts to CSI, Chint, Sunport, and Akcome.
Cell giant Tongwei Group said it had teamed up with Longi in a strategic partnership which will give the latter preferential access to Tongwei’s polysilicon while Tongwei can secure supply of mono wafers from Longi for its cell business.
Additional reporting from Eckhart Gouras and Vincent Shaw.
This article was updated on June 11 to reflect that the mini module on display at the Centrotherm booth was a III-V mini module from Fraunhofer ISE, rather than a perovskite cell.
This content is protected by copyright and may not be reused. If you want to cooperate with us and would like to reuse some of our content, please contact: editors@pv-magazine.com.
What I find interesting about this TOPCon technology is the thin interfaces sandwiched with the silicon cell. This leaves the ability to make a bi or tri model cell structure that can be tuned to use a wider spectrum of light for power production. There has been research on spraying a coating of a perovskite or printing a coating of CIGS that could be used to enhance the power harvest per square foot. Could this be the 30% to 35% efficiency point that would not only make solar PV panels smaller, but more powerful in the space occupied?