After being hit hard by oversupply conditions in the second half of 2016, polysilicon suppliers approached the following year cautiously, on the back of lower demand expectation. These expectations were of course proved wrong, as the year played out to be another record breaker in terms of global installations.
“The biggest difference between 2016 and 2017 was the drop-off in demand that followed the June 30 feed-in tariff (FIT) deadline in China,” explains Johannes Bernreuter, head of Bernreuter Research. “There was not a sharp drop in demand in 2017 – around 12 GW was installed in July, and the deadline for completion of projects in the Top Runner Program was extended, which brought additional demand in the third quarter.”
Installations in China were the factor that confounded most earlier predictions for 2017, and led to tight supply conditions in the third quarter, as polysilicon manufacturers scheduled maintenance for their facilities in anticipation of a drop in demand similar to 2016. “Weaker demand was expected in 2017 because of the lack of transmission lines from sunnier regions in the west of China to the more populated east, and continuing problems with payment of FITs,” says Bernreuter. “Because of this, demand for polysilicon grew faster than supply in 2017.”
So it was continued demand for installations in China that prevented a repeat of 2016’s oversupply situation, almost moving the industry in the opposite direction and causing a shortage. “If you look at the total installation numbers in China in 2017 versus 2016, there is a huge difference of 18 GW. That explains why there was not a similar phenomenon in 2017,” says Bernreuter.

Domestic production
With Chinese companies now comfortably responsible for the largest share of cell and module manufacturing, ambitions are moving upstream. The share of imports in China’s polysilicon supply is slowly decreasing each year, as more factories are brought online. Figures from IHS Markit give Chinese companies a 54% share of global polysilicon output in 2017, an increase from the previous year. “China continues to be the largest polysilicon producer in the world, and Chinese manufacturers are continuously expanding their production capacities,” says Karl Melkonyan, Senior Analyst, Solar Demand at IHS Markit. “This increase is mainly due to significant expansion of Chinese module producers following strong market demand in 2017, as well as the restrictive import duties on U.S. companies hindering polysilicon exports to China.”
According to figures provided by Bernreuter Research, Chinese polysilicon capacity at the end of 2016 was 227,500 metric tonnes (mt), growing to 319,000 mt by the end of 2017. With several new factories set to come online, this capacity could hit 450,000 mt by the end of 2018. “In terms of quantity, Chinese manufacturers are making huge progress,” says Bernreuter. “This supports what I have been saying for a while, that the ultimate goal for China is independence from polysilicon imports.”
While major expansions to China’s polysilicon output have so far been successful in serving the local wafer market, concerns remain over the quality of the polysilicon being produced. This is especially relevant when you look at the increase in market share of monocrystalline products that has played out in recent years – as mono-wafer producers require a higher purity of polysilicon.
“Mono wafer producers are mainly importing high-purity polysilicon from Germany and South Korea,” explains Bernreuter. “Regarding the rapid expansions of Longi and Zhonghuan Semiconductor [both of which exclusively produce monocrystalline products], it remains an open question how they will cover their demand for high-purity polysilicon.”
Imports
So, while monocrystalline silicon continues to enjoy a sizable market share – around 40% by the end of 2017 according to estimates from IHS Markit – Chinese wafer producers will continue to import large amounts of polysilicon. Figures from Bernreuter Research show that China imported 159,000 mt of polysilicon in 2017. Around 45% of these imports came from South Korean producers, with Germany’s Wacker responsible for a further 30% share, and 11% coming from Taiwan.
The large portion of imports from Germany and South Korea are possible thanks to low tariff rates imposed on companies exporting from these countries. Though it may have a long-term goal of independence from polysilicon imports, for now China needs to keep the raw material coming in to meet demand from its ever-expanding cell and module manufacturers.
In November, an investigation by China’s Ministry of Commerce (MOFCOM), launched upon the request of several Chinese producers, concluded that there had been dumping of polysilicon on the part of South Korean manufacturers and adjusted tariffs accordingly.
Now these tariffs stand at 4.4% for OCI – South Korea’s largest producer – and 9.5% for Hankook Silicon Co. Meanwhile, Hanwha Chemical Corporation, the country’s joint second largest producer, actually had its tariff reduced to 8.9%. “South Korean companies have low import tax in China,” explains Melkonyan. “However, the adjustment of import duties on South Korean polysilicon to China might be able to support the local manufacturers in terms of price competitiveness, but the overall effect on the polysilicon segment was not (very) big.”
Germany’s share of imports was kept up thanks to Wacker, which also continues to enjoy tariff-free access to the Chinese market, thanks to an agreement made with MOFCOM requiring it not to sell below a minimum price. The German producer saw a particularly strong 2017, having raised its revenue forecasts multiple times throughout the year, in spite of a chemical accident bringing its 20,000 mt in Tennessee, U.S. offline in September.
U.S. Tariffs
While U.S. manufacturers have continued to be shut out of the market by duties of between 55.4% and 57%, the country was responsible for around 5.5% of imports, primarily from REC Silicon’s fluidized bed reactor facility at Moses Lake, Washington, and from beleaguered polysilicon giant Hemlock Semiconductor.
Hemlock, the largest U.S. polysilicon producer, has been vocal in calling for a reduction to tariffs. It delivered a letter to President Trump in January requesting that a resolution be included in the announcement on the Section 201 case, which went on to place tariffs on Chinese cell and module imports to the U.S.
While this, and China’s need for imports to satisfy all demand, could result in a reduction, analysts do not seem optimistic about the Chinese government’s willingness to negotiate.
“For the U.S. polysilicon companies attempting to sell again in the China market, this is not good news,” explains Melkonyan. “First, it will not facilitate the removal of the current barriers to export U.S. polysilicon into China. Second, the announcement made recently by the U.S. administration is forecast to have a negative effect, slowing down PV demand in the U.S., which could indirectly impact on reducing the total demand for polysilicon in 2018.”
And it also seems likely that the prospect of a short-term polysilicon shortage would not be enough encouragement for China to provide access to U.S. suppliers. “There was a slight shortage of poly inside China in Q3, and you can of course argue that higher tariffs on imports exacerbate this. If U.S. producers had been able to import more volume at a lower tariff, or no tariff, there wouldn’t have been the shortage situation inside China,” says Bernreuter. “But the reaction of Chinese companies to Trump’s announcement was muted and calm, my impression is they don’t have a major problem with the new tariffs.”
Overall then, the volume of polysilicon imported to China has not fluctuated greatly, while imports have fallen as a percentage due to China meeting more demand domestically. “I would say that the growth of imports is slowing down, not that the absolute amount imported is decreasing,” says Bernreuter. “China is replacing additional demand for polysilicon imports through domestic production.”
Expansion plans for production outside of China among polysilicon producers are few and far between at the moment, which would support the theory that demand for imports is stagnating. South Korea’s OCI is one of the only companies known to be contemplating expansion outside of China, with plans for a new facility in Malaysia still ‘under review’ at the time of writing this article.
“You have to look at the expansion plans of the main importers,” continues Bernreuter. “Wacker is improving capacity a little bit every day through debottlenecking and other improvements, but there is no plan for a new facility. OCI is planning an expansion in Malaysia, but that will probably come online at the end of 2019 at the earliest.”
Wafer
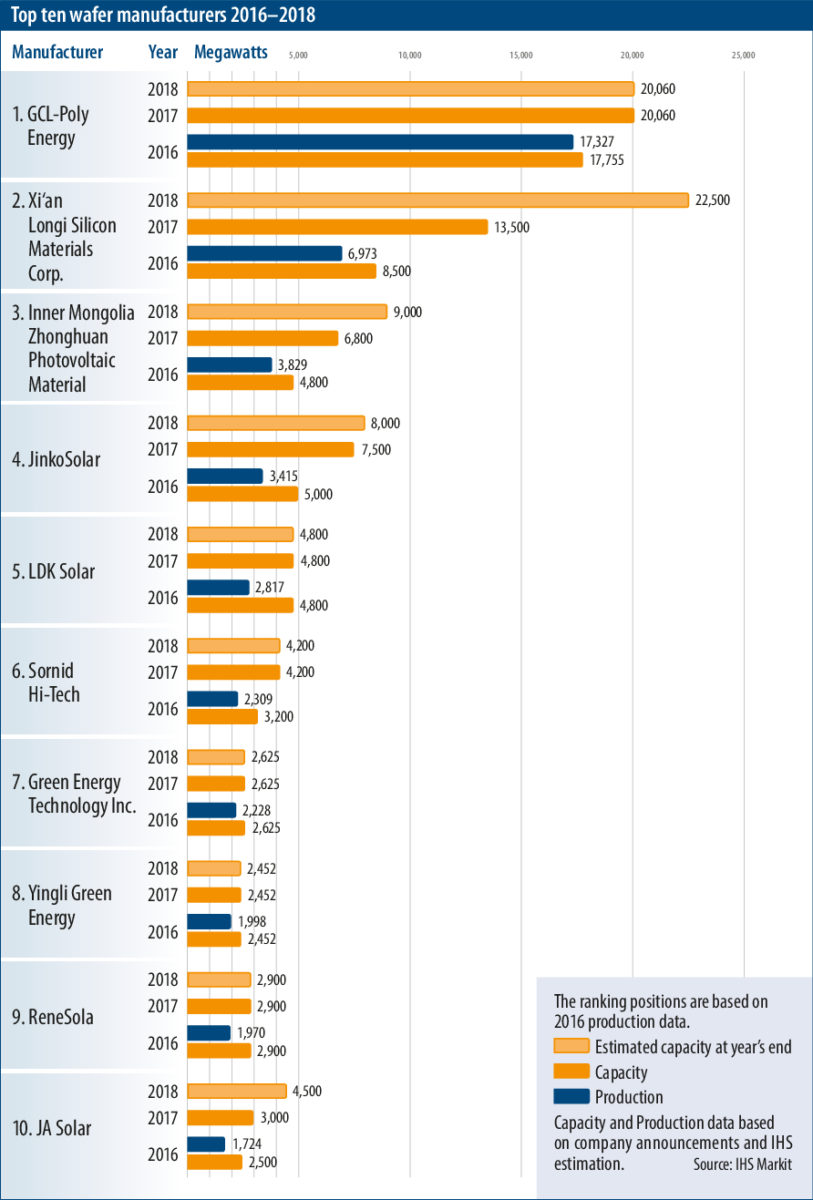
The market for silicon wafer, meanwhile, has continued to be defined by the rapid gain in the market share of monocrystalline silicon. The continued presence of Xi’an Longi Silicon Materials in the number two spot exemplifies this shift, and the company recently announced further plans to increase its wafer capacity to 45 GW by 2020.
“The main reasons for the increasing share of monocrystalline wafer are the average price decline of mono c-Si, which has narrowed the gap in cost per watt between mono and multi c-Si, and increasing demand for high efficiency modules in Europe and the U.S., as well as in China with the Top Runner Program,” says Melkonyan.
Most analysts though do not expect the share of mono c-Si to overtake that of multi, or indeed to grow much further beyond its current level. “The growing demand of monocrystalline does not mean the demise of multicrystalline, which is expected to continue to account for most of the market,” continues Melkonyan. “The use of diamond wire saws in multicrystalline wafer production is increasing wafer efficiency, and reducing kerf and production costs, which obviously helps to make it attractive again. However, full adoption of this cutting technology will still take some time.”
Longi’s announcement of this ambitious expansion plan has already led independent solar analyst Corrine Lin to predict an oversupply situation for mono wafer in the second half of 2018. On the basis of mono wafer capacity expanding from 44.5 GW to 73 GW this year, total mono wafer capacity will far outstrip predictions of demand for the technology, based on a 40% share of a conservative demand estimate of 95–105 GW for 2018.
Karl Melkonyan also points out the importance of India’s recent policy announcements to the global wafer market: “The recent announcements in India regarding the AD duties and other safeguard import taxes, are expected to impose severe barriers for multicrystalline products, which could accelerate price decline for this technology, and reduce demand for monocrystalline products,” he explains. “Since monocrystalline capacity is expected to continue growing in H2 2018, this might generate a situation of oversupply. It all really depends on policy developments in India in the coming months.”
Into 2018
Analysts are once again divided over global demand predictions for 2018, with more conservative estimates expecting a similar level to 2017, while others point to China’s persistent defying of expectations in recent years, and predict further growth. Based on polysilicon supply, Bernreuter Research is sitting firmly on the growth side of the fence: “We have run three preliminary scenarios with global PV installations of 110, 115, and
120 GW respectively. With 110 and 115 GW there would be polysilicon oversupply. With 120 GW the polysilicon market would be largely balanced (if there is strong inventory build-up for 2019, oversupply would not be an issue in the 115 GW scenario either),” says Bernreuter. “We expect a 120 GW market, with approximately 65 GW of new installations in China.”
This content is protected by copyright and may not be reused. If you want to cooperate with us and would like to reuse some of our content, please contact: editors@pv-magazine.com.
Great analysis – thanks for the in-depth market details!